preface
China is a big country in casting production, the current degree of automation after casting cleaning is low, and belongs to high risk, high pollution (large amount of dust), high energy consumption casting production bottleneck process, with the development of science and technology, post-casting cleaning and polishing more and more attention, but after casting cleaning cutting, grinding link automation is weak, need to improve, many enterprises still stay in the form of manual cleaning, thus causing many problems, high labor intensity, insufficient labor, recruitment difficulties, occupational diseases, safety hazards; High energy consumption, large dust, harsh on-site environment; Therefore, the mechanization and automation of cutting, grinding and cleaning after casting have become an inevitable trend of development.
1 Overview of post-casting cleanup
Post-casting cleaning refers to a set of rough machining systems for casting finishing, such as shell clearing, spruer cutting, casting separation, grinding, welding repair, etc., including equipment, logistics, and supporting intelligent auxiliary applications for casting sprue, parting wire cutting, grinding, spruer residue grinding, casting surface grinding.
1.1 Cleaning after casting
Post-casting cleaning can be divided into two production links, pre-order and post-sequence, the pre-order mainly includes conjoined casting separation, spruer cutting, parting line pre-cleaning and other work, the way is flame cutting, plasma cutting, casting separator, carbon arc gouging and other forms, the processing form is generally manual cleaning
The management method is the mainstay, and a small number of series manipulators and other equipment forms are used; The subsequent sequence includes casting cutting, casting grinding, casting surface oxide scale cleaning, compared with the previous sequence, the workload is large, the difficulty is high, the technical difficulty is high, and auxiliary intelligent functions need to be added. Supporting intelligent applications include error correction and positioning technology (correction point/line laser, contact automatic trajectory compensation, spatial positioning technology), flexible technology (light stiffness flexible technology, high stiffness flexible technology) and system integration. The cutting and grinding process of the subsequent sequence is divided into two working conditions: easy to achieve and difficult to achieve:
(1) Easy to realize working conditions
(1) Small and medium-sized castings, the material is gray iron, ductile iron, the casting is generally high casting accuracy, small deviation, small sprue, parting line, and low equipment rigidity.
(2) Small and medium-sized castings (non-ferrous metals including copper, aluminum, etc.), high casting accuracy, low equipment rigidity, general equipment is easy to achieve.
(2) It is not easy to achieve working conditions
(1) Special material (three high): with high viscosity, high heat, high hardness characteristics (including: nickel, chromium, silicon, molybdenum, manganese and other elements) such as turbocharger series, railway series of transmission shafts, wear parts, etc.
(2) Medium and large castings and cast steel materials, the spruer parting line is large, the casting deviation is large, and the equipment rigidity and processing stroke requirements are high, such as railway pillows, side frames, hook and tongue hook bodies, automotive industry bridge shells, internal combustion engine cylinder blocks, pump valves and other castings, cutting and grinding is difficult.
(3) Surface cleaning of other types of oversized parts, removal of residues after fire cutting of large steel castings, surface treatment of wind turbine hubs and other surface cleaning problems of large castings.
1.2 Technical route form of cleaning after casting
In recent years, the grinding equipment that has appeared in the domestic and foreign markets mainly includes machine tool form, tandem (three-joint/six-joint) manipulator form, non-standard form, and mixed structure form. Now for various forms of grinding equipment and supporting intelligent applications
The technology is explained so that foundry companies can select the right grinding equipment for themselves:
(1) Machine tool form: suitable for grinding certain complex shape, small shape, medium casting (ductile iron)
(1) Movement mode: linear axis movement mode, horizontal structure form of lead screw guide rail, and corresponding increase in the volume of processing larger casting equipment;
(2) Grinding spindle: electric spindle, consumable size within a reasonable range (diamond consumables must have a certain linear speed, the larger the size, the longer the life of the consumables);
(3) The flexibility and flexibility of the grinding workpiece are insufficient, and it is difficult for the machine tool to adapt to processing if it exceeds a certain size of castings;
(4) A large amount of iron powder will be produced during the grinding process of castings, and these iron powder will penetrate into the linear motion mechanism of the machine tool with the movement of the machine tool, causing damage to the parts, and the size of the machine tool is large, and a lot of manpower will be consumed during the maintenance process;
(5) The equipment rigidity is higher than that of the tandem manipulator, suitable for general parting line and spruer grinding, not suitable for steel casting cutting, grinding steel casting riser need to slow down the processing speed, energy consumption is relatively high, spindle power is generally more than 20 kilowatts.
(2) Tandem manipulator (three-joint/six-joint) form: suitable for certain complex shape, small shape, medium casting low strength grinding (ductile iron)
(1) Flexibility, the biggest advantage is high flexibility, suitable for logistics transshipment;
(2) The rigidity of the equipment is insufficient, it is not suitable for grinding of risers and large parting lines, and needs to be cleaned in layers, and the efficiency is reduced;
(3) The end bearing force of the manipulator is small, long-term work will cause the wear of the manipulator, the life is reduced (one to two years), the casting produces a large tangential grinding force during the grinding process, these grinding forces will act on the tandem manipulator, causing the wear of the gears of the joint reduction system, resulting in precision
loss of degree and reduction of service life;
(4) The life of the consumables is reduced, the size of the consumables used is small, and the high speed is required to compensate for the linear speed, resulting in low consumable life.
(3) Non-standard form: for fixed workpiece processing equipment is simple, high efficiency but single function, can only solve a certain aspect of the needs of castings, it is difficult to achieve universal equipment, difficult to group lines, suitable for large quantities and few types of castings, such as stamping form.
(4) Hybrid high stiffness form
(1) The main equipment is a new mechanism of grinding and cutting integrated processing robot with compact structure, strong reconfigurability and high rigidity;
(2) It solves the problem of insufficient flexibility of traditional machine tools and low rigidity of tandem robots;
(3) The efficient grinding and cutting integrated processing of special-shaped and complex castings of different specifications solves the common problem of “small pieces do not dry quickly, medium parts do not dry well, and large parts cannot dry”.
In summary, the first three forms of equipment have different degrees of defects, the company’s independent research and development of hybrid high rigidity robot can meet the cutting and grinding of all kinds of small, medium and large castings, to achieve the integration of cutting and grinding, the completion of cutting and grinding sequence, to save manpower, reduce logistics, reduce energy consumption,
Save space, fast efficiency, short return period, high comprehensive income; The company’s products include closed, open, pass-through and other types of products and error correction positioning technology (fixed/line laser, contact automatic trajectory compensation, spatial positioning technology), flexible technology (light stiffness flexible technology, high stiffness flexible technology) and system integration technology combined and applied to the practice, customer economic benefits have been significantly improved.
2 Technical requirements and equipment requirements for cleaning after casting
2.1 Technical requirements for cleaning after casting
(1) Classification and application of tools/consumables
(1) Resin: resin slices, brown corundum grinding wheel, zirconium corundum grinding wheel are used for casting grinding, and they will be continuously lost during the grinding process and need to be adjusted at any time The position of the entire grinding wheel ensures grinding accuracy and is often used in four-sided grinding equipment. The grinding accuracy is low, and the required motor power is large, the energy consumption is high, and the dust is large.
(2) Diamond: diamond slices, diamond grinding discs, commonly used types of equipment, cutting and grinding without loss, high processing accuracy.
(3) Others: alloy saw blade can be used for non-ferrous metal cutting and milling.
(2) The main functional parts of the equipment
(1) Equipment motion power mechanism: the lead screw guide rail brand selects well-known brands, quality assurance and after-sales service, and the structure meets the dustproof grade and dustproof
Design form.
(2) Equipment cutting and grinding function mechanism: the spindle form is divided into electric spindle and mechanical special spindle, the application conditions of the two are different, and the maintenance cost is different,The electric spindle has high machining accuracy and low bearing capacity, which is suitable for the field of finishing machining, and the heat generation is large when used for casting grinding, the spindle is easy to break, and the electric spindle is made into irreversible damage; Under the residual working condition of centimeter-level riser, the failure rate is higher. The mechanical spindle has low speed, high stability, high bearing capacity, and castings fly The change of edge burr state has low influence on the mechanical spindle; Combined with the high-rigidity hybrid arm structure, it can quickly and effectively grind to remove the residual of the centimeter-level riser of the casting.
(3) Technical requirements for casting cutting and grinding
(1) Equipment stiffness is a necessary condition for equipment to be cleaned and polished after casting, equipment rigidity, fast processing speed, high efficiency and vice versa Inefficient.
(2) The form of consumables, including the type of consumables, the size of consumables, no loss when cutting and grinding of diamond consumables, no dust output of tools, and the larger the size of consumables The lower the cost, and at the same time meet the accuracy requirements of cleaning roughing after casting.
(3) The speed of the consumables cutting and grinding line is an important parameter of the consumables cutting and grinding process, and what kind of consumables need to correspond to the relevant line speed in order to maximize it Ensure the service life of consumables and ensure processing efficiency.
2.2 Equipment requirements for cleaning after casting
2.2.1 Basic Requirements
(1) Easy to achieve working conditions, normalized small and medium-sized workpieces (cast iron and non-ferrous metals) currently on the market equipment basically meet the needs of grinding, customers can choose according to their own product characteristics, but to consider from a long-term perspective, such as late casting product changes including casting size, material, and casting process and other aspects, whether the existing equipment meets the later needs, to reduce the later equipment purchase cost.
(2) It is not easy to achieve working conditions, special materials (three high) have high viscosity, high heat, high hardness characteristics (including: nickel, chromium, silicon, molybdenum, manganese and other elements) small and medium-sized parts cutting, grinding, the use of closed equipment cutting and grinding integrated robot (as shown in Figure 1).
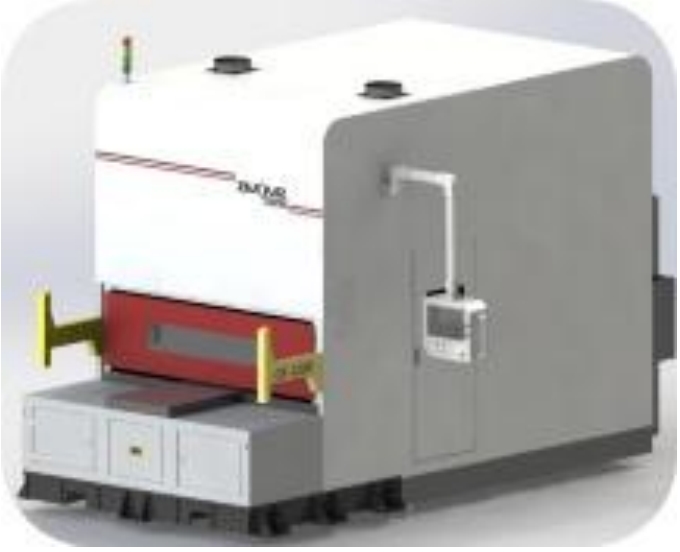
Figure 1 Closed, high-stiffness grinding and cutting universal robot
2.2.2 Device Introduction
(1) Suitable for small cast steel, cast iron and non-ferrous material castings
(1) Product features
a. High rigidity: the rigidity of the hybrid manipulator is more than 20 times that of the tandem manipulator;
b. Spindle form: special spindle system for high stiffness grinding, fast processing speed and high precision;
c. Flexibility: multi-axis, the axial movement of the equipment is five + two-axis auxiliary shaft holes;
d. Tooling/fixture: mechanical locking, firm and safe, easy to replace and low cost.
e. Consumables application: the equipment grinding is stable, the consumables have a long service life, and the cost of a single consumables is low.
f. Low energy (power) consumption: the normal operation power of the equipment is 3~5 kW.
g. Intelligent configuration: laser (point line) detection correction, automatic trajectory compensation function.
h. Installation and commissioning: on-site installation and commissioning week
Short period and short teaching programming time.
(2) Application cases
Table 1 shows the cutting and grinding application cases and application industries of cast steel, cast iron and non-ferrous metal castings.
(2) Suitable for medium and large steel castings
It is not easy to realize medium and large castings and steel casting materials, the spruer parting line is large, the casting deviation is large, the equipment stiffness and processing stroke requirements are high, the open type high stiffness grinding and cutting general robot (as shown in Figure 2) is selected, multi-head form, cutting, grinding integrated application, auxiliary error correction positioning technology can effectively solve the spruer cutting, grinding.
(1) Product features
High rigidity grinding and cutting universal robot with
Set multiple tool heads, axial flexibility, effectively solve the grinding problem of medium and large castings, realize the integration of cutting and grinding, with high rigidity, high load, high flexibility, low energy (power) consumption characteristics, has solved the internal combustion engine cylinder block,
Medium and large pieces such as pillows and bridge shells are automatically cut, polished, and applied to the site.
a. Multi-tool magazine combination form, cutting and polishing one
The body refinement is completed in one sequence, and the efficiency and comprehensive cost performance of multiple sequence and one sequence are doubled;
b. Multi-axial (twelve motion axes), high degree of completion, fixed mechanism (tooling) configuration flip mechanism;
c. Exclusive design: single, double station, pass-through and other forms of efficiency improvement;
d. The separate design of the equipment and the turntable has high bearing capacity, which solves the problem that large castings are difficult to polish due to weight restrictions;
e. High rigidity, obvious structural advantages, effective removal of large spruer grinding and cutting, high efficiency, high precision, low energy consumption;
f. The overall area of the stand-alone and supporting production lines is small, saving space and reducing logistics;
g. Suitable for: steel casting, iron casting, aluminum casting, non-ferrous metals, precision casting casting cutting and grinding applications;
h. One person and multiple machines to solve the problem of insufficient manpower and difficulty in recruitment;
i. Error correction and positioning technology: point/line laser, contact automatic trajectory compensation, spatial positioning technology.
(2) Application cases
a. Supporting intelligent applications: point/line laser, as shown in Figure 3;
b. Case of large-scale cylinder production line, see Figure 4;
Table 1 Examples of cutting and grinding applications for cast steel, cast iron and non-ferrous metal castings

Figure 2 Open high-stiffness grinding and cutting universal robot
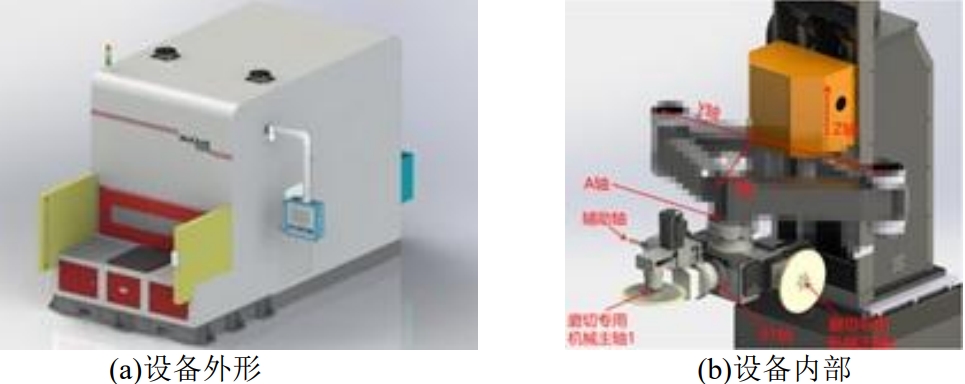
Figure 3 Laser inspection scene of point/line
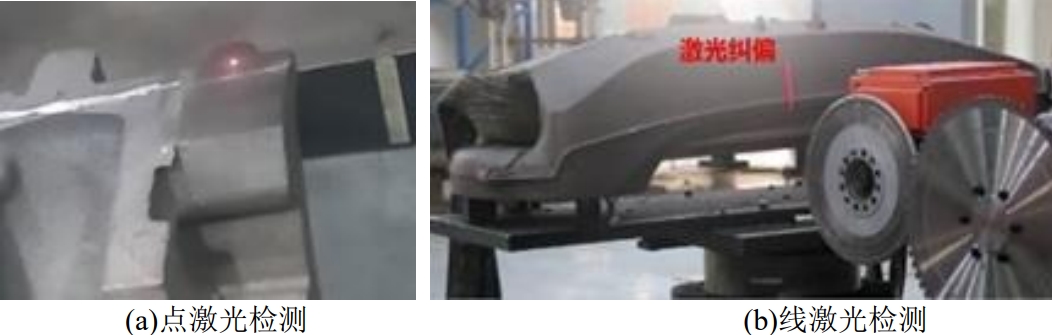
Figure 4 Application example of large cylinder production line
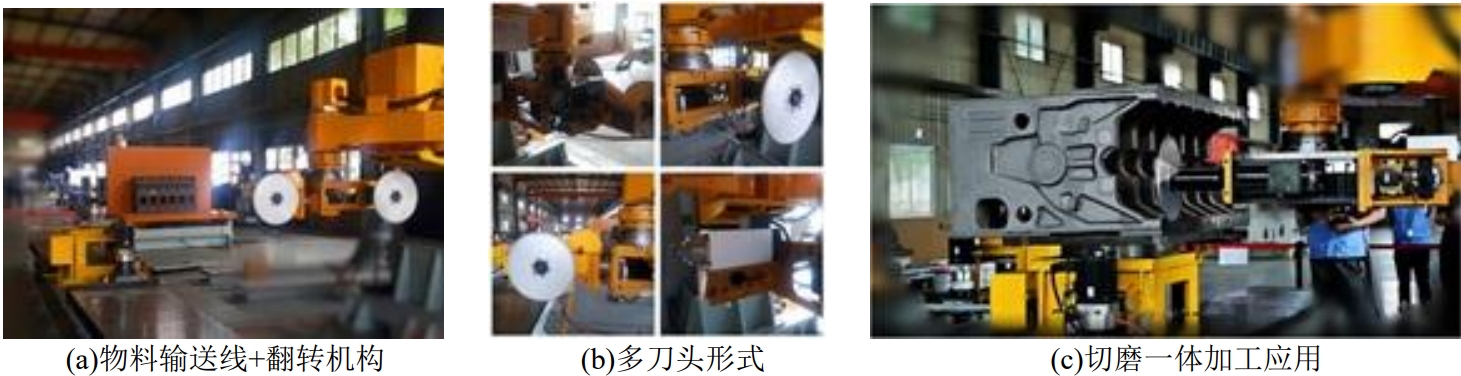
(3) Suitable for rapid processing of round castings (such as brake drums, hubs, pressure plate series)
(1) Straight through type is selected, and the logistics line inside the equipment is automatically loaded and unloaded, and the rapid grinding of castings is efficient and fast, as shown in Figure 5.
(2) Equipment characteristics
a. Multi-axis, flexibility: X, Y, Z, A, B, W, U, V form (A, B is the grinding wheel composite axis, W axis is the workpiece rotation axis, U-axis power head milling axis, V is the workpiece push axis);
b. Multi-function integration: the top milling power head mechanism and grinding spindle work at the same time, the processing speed is fast, and the average single piece processing efficiency is 6~8 seconds;
c. Human-machine efficacy ratio: 4~8:1, cutting and grinding universal, cutting and grinding integration.
(4) It is suitable for spruer grinding and oxide scale cleaning of other large castings
(1) High rigidity flexible grinding technology, mainly used to solve large casting riser stumbles, sticky sand, succulent working conditions, equipped with auxiliary shaft floating mechanism suitable for casting series hole grinding; The mechanical spindle floating mechanism is suitable for flat and arc grinding. Combined with spatial origin positioning technology, force feedback mechanism, force
Remote control technology, teaching programming, automatic trajectory compensation, laser dot line detection.
(2) Low rigidity flexible grinding technology, mainly used in tandem manipulator equipment, with radial floating mechanism, axial floating mechanism, mainly used in casting surface position cleaning, such as wind turbine fan blade casting grinding, hole position grinding and casting cavity skin cleaning, such as machine tool casting grinding.
(5) Supporting intelligent application technology
(1) Error correction and positioning technology
a. Contact automatic trajectory compensation technology: contact detection form, low cost, light weight, easy installation, simple control program, suitable for working in high dust environment, not affected by dust, high detection accuracy, not affected by the surface of castings.
b. Point laser detection technology: advantages: relatively low cost, simple operation; Disadvantages: Low data collection efficiency and poor data collection accuracy.
c. Line laser detection technology: high data collection efficiency, high accuracy, relatively high cost, complex operation, high requirements for personnel.
d. Spatial positioning technology: force-controlled remote operation technology combined with spatial origin positioning technology provides the best accuracy and operational convenience. Force-controlled remote operation is the active control unit to drive high-stiffness equipment or tandem manipulator driven unit to complete the grinding work.
(2) Flexible technology includes high stiffness flexible technology and light stiffness flexible technology
High stiffness flexible technology is Tianjin Zhongyiming Technology Co., Ltd. combined with the high stiffness characteristics of hybrid structure, developed another form of high stiffness flexible grinding technology, applied to the surface of casting large grinding volume removal conditions, including fire cutting after spruer residue, spruce residue, succulent, sticky sand, etc
Working conditions, greatly improve processing efficiency.
Light stiffness flexible technology is mainly used for casting skin treatment, not suitable for high-strength grinding, such as the presence of meat on the surface of castings, riser residues and other working conditions, light stiffness flexible grinding efficiency is low, equipment load is too high, equipment service life is reduced.
a. High stiffness flexible technology – high stiffness mechanical flexible grinding and application, see Table 2.
b. Light stiffness flexible technology – manipulator floating grinding technology and application, see Table 3.
Table 2 High stiffness flexible technology – high stiffness mechanical flexible grinding applicationexamples
type | name | Condition type | Application scenarios |
High stiffness | Auxiliary shaft floating mechanism | Casting series hole grinding | Inner cavity castings |
High stiffness | Mechanical spindle floating mechanism | Flat and curved surface grinding | Machine tool castings, residual after fire cutting |
Table 3 Light stiffness flexible technology – application example of manipulator floating grinding technology
type | name | Equipment selection | Application scenarios |
Light stiffness | Radial floating mechanism | Tandem manipulator | Large casting scale cleaning |
Light stiffness | Axial floating mechanism | Tandem manipulator | Hole grinding and cleaning of the inner cavity of castings |
Method 1: The main grinding equipment and manipulator are combined, and the detection function is configured to form an automated production line;
Method 2: The combination of main grinding equipment and truss manipulator is matched with the form of automatic grinding production line of logistics line, which is suitable for the integrated application of cutting and grinding of small and medium-sized castings.
Pass-through automatic production line form: only need to connect with the incoming line to solve the grinding of round castings, connect the production line with the post-cleaning line to save a lot of intermediate links, improve efficiency, increase production capacity, and reduce operating costs. Open automatic production line form: the multi-head function simplifies multiple processes into one sequence, cooperates with the conveyor line to process medium and large castings, and uses detection technology to solve casting deviations to ensure processing accuracy, such as large-scale cylinder production system applications, railway system pillow products cutting and grinding integrated applications, bridge shell casting cutting and grinding integrated applications. Application form: (4) The remote MES system builds a networked integrated system in order to realize the overall data interaction between MES and the equipment monitoring system, and adopts a hierarchical and optimized network strategy. The network layering design has the characteristics of scalability, elimination of redundancy, improved performance, network security and reliability, and manageable maintenance. According to the actual network distribution on site, the system is implemented hierarchically, divided into MES and ERP-based management layer, HMI-based on-site monitoring layer, PLC (or
Motion controller) is mainly designed for a three-layer network such as the on-site control layer. The MES system and monitoring layer adopt the integration mode of intermediate database, which effectively solves the problem of data interaction between different development platforms. Through the intermediate database to store the data that needs to be interacted with between the systems, to achieve the matching of the unified definition of the shared data format and related attributes, and complete the data interaction in the operation process of the intermediate database. At the same time, the on-site production plan is customized according to the order plan, and the process data monitoring and the visualization of the production kanban at the workshop level are carried out. Realize the interconnection of field devices or field instruments for process automation and manufacturing automation, and cover the communication network from the monitoring management to the production site and field control equipment.
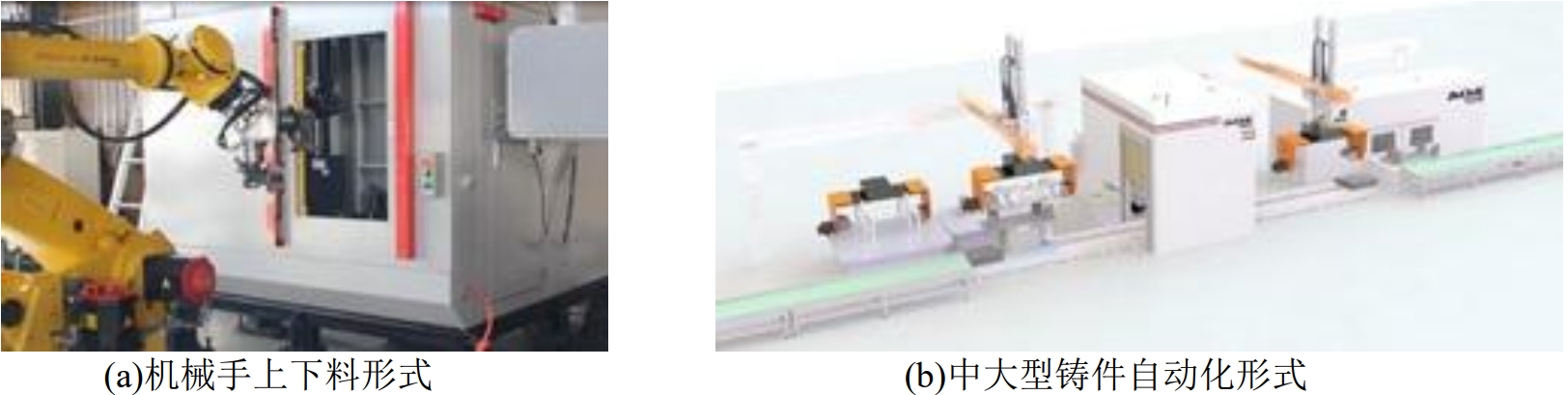
Figure 6 Examples of intelligent integrated applications
2.3 Precautions for equipment selection after casting
(1) Sample test, the actual test effect and efficiency of the sample to reflect the actual application ability of the equipment.
(2) Equipment parameters, process parameters, grinding speed, equipment load, equipment energy consumption, dust removal and dust prevention, etc.
(3) Versatility and flexibility: covering a variety of products, high polishing completion, reducing processes and reducing input.
(4) Programming efficiency: The reason why the device has fast programming ability is that it has core algorithms, and vice versa.
(5) Applicable materials: grinding and cutting equipment should adapt to workpieces of various materials, such as heat-resistant steel, high-nickel steel, cast steel, cast iron, non-ferrous metals, etc.
(6) Equipment processing accuracy and surface quality.
(7) Equipment functional parts configuration and equipment dustproof performance.
3 Conclusion
The company has been quietly working in the field of casting grinding and cutting for more than ten years. Taking the industry demand as the traction, the self-developed high-rigidity grinding and cutting integrated processing robot is completely different from other forms This product breaks through the mode of tandem robots and machine tool products, and solves the constraints on industry capacity, safe production and production
The technical bottleneck of environmental governance has promoted the transformation and upgrading of traditional manufacturing industry and achieved significant social benefits. Foundry enterprises are called upon to improve the casting process while cleaning the equipment after selection, and integrate the cleaning after grinding and cutting of castings with the casting process, so as to achieve a win-win situation.