1. Introduction
In the field of high – speed train technology, the gear transmission system plays a crucial role in transmitting power and ensuring the smooth operation of the train. However, due to various factors such as heavy loads, high speeds, and complex operating conditions, the gear teeth may experience wear, pitting, and breakage faults. These faults can significantly affect the performance and safety of the gear transmission system, and even lead to train accidents. Therefore, it is of great significance to study the nonlinear dynamic characteristics of the gear transmission system with tooth breakage faults.
The research in this paper focuses on the CRH2 type EMU traction gear transmission system. By establishing a 5 – degree – of – freedom bending – torsion – axial coupling dynamic model that takes into account the axial, lateral vibration, and torsional characteristics of the helical gears, the dynamic behavior of the system under tooth breakage faults is analyzed. Through numerical simulation and theoretical analysis, the bifurcation characteristics and dynamic response of the system are studied, providing a theoretical basis for the design, fault diagnosis, and maintenance of high – speed train gear transmission systems.
2. Dynamic Model Establishment
2.1 Gear System Mathematical Model
The 5 – degree – of – freedom bending – torsion – axial coupling dynamic model of the helical gear transmission system is shown in Figure 1. The model includes the support stiffness and damping of the two gears, the torsional displacement of the meshing gears, the meshing stiffness and damping, the torque applied to the gears, the backlash, and the meshing error.
Based on the d’Alembert principle, the differential equation of the bending – torsion – axial coupling vibration system of the helical gear transmission can be expressed as follows:
where represents the torsional displacement of the two gears in mesh, is the equivalent mass of the gear pair, is the average value of the system transmission load, represents the mass of the two gears, is the equivalent external excitation load, is the equivalent internal excitation load, and represents the backlash function of the two gears in mesh.
The backlash function is expressed as:
The time – varying meshing stiffness of the gear is expressed in the form of a Fourier series as:
where is the fundamental frequency of gear meshing, is the average meshing stiffness of the gear teeth, and and are the Fourier series expansion coefficients.
The meshing transmission error of the gear teeth is expressed as:
where is the average error, is the error amplitude, and is the phase angle.
2.2 Dynamics Equation Dimensionless
By taking the dimensionless time , where , the dimensionless excitation frequency , and using the characteristic dimension as the nominal scale, the dimensionless equations of the system can be obtained through dimensionless processing of the original equations. The dimensionless displacement and velocity variables are defined as and , respectively. The dimensionless equations of the system are as follows:
where , , and .
2.3 Stiffness Fault Model Establishment
When a gear tooth breakage fault occurs, the meshing stiffness at the fault location decreases. According to the relevant standards, the average meshing stiffness can be calculated as , where is the average total stiffness of the gear in the end face and is the tooth width. It can be seen that the tooth width is proportional to the average meshing stiffness. When a single tooth breakage fault occurs, the average meshing stiffness of the gear decreases.
Based on the Fourier series expression of the time – varying meshing stiffness of the gear, the dimensionless expression of the time – varying meshing stiffness with tooth breakage fault is , where is the tooth breakage fault function, is a periodic pulse function with a period of 1, and is a negative value less than 1, and the absolute value of represents the degree of tooth breakage fault.
3. The Influence of Tooth Breakage Fault on System Stability under Variable Excitation Frequency
3.1 Three – Dimensional Bifurcation Diagram in the (,) Parameter Plane
By taking the tooth breakage fault amplitude parameter as the research object and ignoring the influence of other basic parameters of the system, the three – dimensional bifurcation diagram of the system in the (,) parameter plane is obtained through numerical calculation, as shown in Figure 2.
When the tooth breakage fault amplitude is small, as the system excitation frequency increases, the overall motion form of the system shows a process of changing from periodic motion to chaos through a doubling sequence and then gradually degenerating into stable periodic motion. When is large, the instability characteristics of the system are obvious, and the system mostly exhibits chaotic or quasi – periodic motion. When the excitation frequency is fixed, as the fault degree increases, the system quickly changes from stable periodic motion to chaotic instability.
3.2 Global Bifurcation Diagram under Different Tooth Breakage Fault Amplitudes
Taking the dimensionless meshing frequency of the system as the control parameter and selecting the interval of (0.0, 3.0), the global bifurcation diagrams of the system under different tooth breakage fault amplitudes are obtained through numerical simulation analysis, as shown in Figure 3.
When , that is, when the gear system has no fault, as the system excitation frequency increases, at , the system bifurcates from periodic 1 motion to periodic 2 motion through doubling, and at , the system degenerates back to periodic 1 motion. That is, in the interval of , the system is in stable periodic motion, and there are bifurcation jump points during this period, and the gear meshing state is good with small motion impact. At , the system enters chaotic motion through Hopf bifurcation, and in the interval of , the system exhibits chaotic motion mixed with periodic multi – periodic motion and periodic windows. At , the system degenerates to periodic 2 motion through inverse Hopf bifurcation and then enters stable periodic 1 motion through inverse doubling bifurcation.
By comparing Figures 3(a), (b), (c), and (d), it can be seen that the larger the fault amplitude , that is, the greater the degree of tooth fault, the more obvious the instability characteristics of the system, especially the significant impact on the periodic motion of the system. The periodic motion of the system is transformed into multi – periodic, quasi – periodic, or chaotic motion due to the influence of tooth breakage fault, and the dynamic characteristics of the system become more complex.
3.3 Phase Diagrams and Poincaré Mapping Superposition Diagrams under Different Tooth Breakage Fault Amplitudes
Figures 4, 5, and 6 show the system phase diagrams and Poincaré mapping superposition diagrams under different tooth breakage fault amplitudes when , , and , respectively.
In Figure 4 (), when , the system exhibits stable periodic 1 motion without fault, while when , , and , the system shows periodic 10 motion. This indicates that with the increase of the tooth breakage fault amplitude, the periodic 1 motion of the system is transformed into multi – periodic motion, and the stability of the system decreases.
In Figure 5 (), the system phase diagrams and Poincaré mapping diagrams under different tooth breakage fault amplitudes all show that the system is in a chaotic motion state, and by comparing the graphs, it can be seen that the motion characteristics in the chaotic state are slightly affected by the tooth breakage fault.
In Figure 6 (), when , the system exhibits stable periodic 2 motion without fault, and as increases, the system enters quasi – periodic 2 motion under the influence of the tooth breakage fault.
Overall, the influence of the tooth breakage fault amplitude on the system is mainly concentrated in the low – frequency and high – frequency regions. In the low – frequency region, the influence of the tooth breakage fault is that the system changes from single – periodic motion to multi – periodic motion, and in the high – frequency region, it is manifested as the transition from periodic motion to quasi – periodic motion.
4. Conclusion
The research in this paper shows that the tooth breakage fault makes the dynamic behavior transition process of the gear transmission system more complex, especially having a more significant impact on the periodic motion. Compared with the fault – free state, the stable single – periodic motion of the system is affected by the fault and evolves into multi – periodic and quasi – periodic motion. In the chaotic region, the fault has no significant impact on the dynamic characteristics of the system.
The results of this study can provide a theoretical basis for the design and parameter optimization of gear systems operating in complex environments, as well as for fault diagnosis and maintenance. By understanding the nonlinear dynamic characteristics of the gear transmission system under tooth breakage faults, appropriate measures can be taken to improve the reliability and safety of high – speed train gear transmission systems.
Future research can focus on further exploring the influence of other fault types and multiple faults on the dynamic characteristics of the gear transmission system, as well as developing more accurate fault diagnosis and prediction methods. Additionally, experimental verification of the theoretical results obtained in this study can be carried out to enhance the practical application value of the research findings.
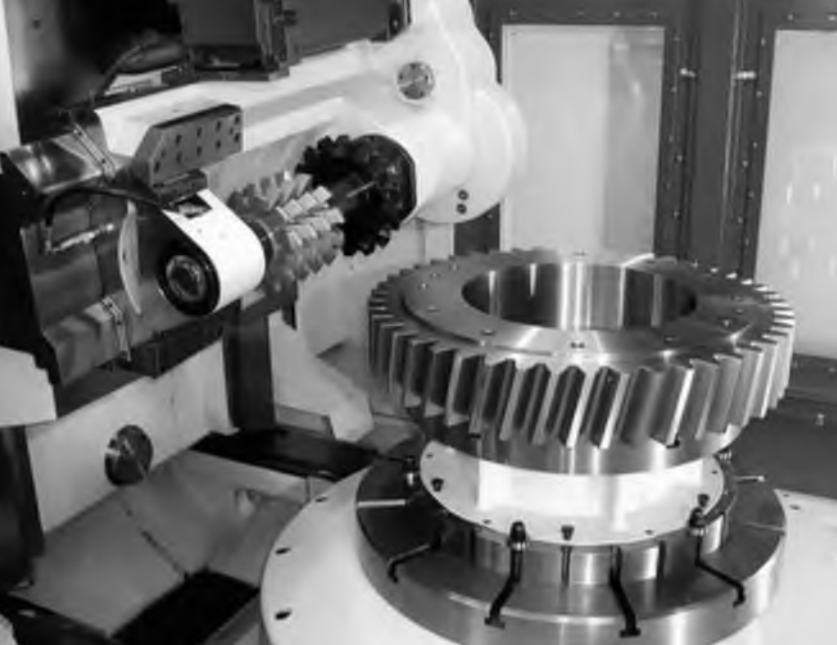