Automobile rear axle (also known as drive axle) refers to the rear drive shaft and related components used to transfer the kinetic energy of the automobile. The automobile rear axle needs to bear the weight of the automobile rear axle, but also to reduce the speed, drive the vehicle and realize the half axle differential motion. The working principle of the automobile rear axle is: the engine converts the heat energy generated by fuel combustion into kinetic energy, i.e. torque, which is gradually reduced in the conduction process of the clutch, reducer and other devices, and the torque is continuously increased; finally, the torque is transmitted to the wheel through the half bridge for driving the motor car wheel. The driven spiral bevel gear and the driving spiral bevel gear on the main reducer work together to form a gear pair to change the torque transmission direction. As shown in the figure is the schematic diagram of the rear axle (drive axle) of a certain type of automobile.
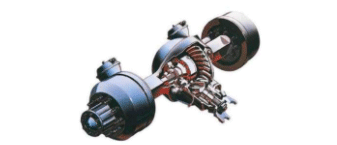
As the main transmission part of the main reducer system, the main and secondary spiral bevel gears need to bear the impact of variable amplitude load under the high temperature and harsh working environment for a long time. The urgent desire of consumers for the safe and stable driving of vehicles makes the main engine factory put forward more and more strict requirements for the product quality, accuracy and mechanical properties of gears.
Germany, Japan and other developed countries began to study the gear forming process early, and the technology is more advanced. China’s relevant research began in the 1970s. Traditionally, the gear tooth is machined by cutting technology, which not only cuts off the continuous fiber structure inside the metal and affects the structural strength of the gear, but also takes a long time to process a single piece and wastes a lot of raw materials. In the later stage, with the continuous progress of material processing technology, various new technologies have been introduced into the gear processing and production.
Kondo K et al. Kondo K et al. Used the cold precision forging process to process the gear with boss and obtained the metal flow law in the forming process; Doege e proposed and proved the possibility of forming spur gear and helical gear with the hot die forging process on the cross opening and closing machine; the possibility of Cai J gear and helical gear; CAI J applies the cross combination of floating and immovable dies, inclined and plane dies to the forging production respectively. By observing the metal flow and stress-strain conditions under different combinations of dies and dies, it is concluded that the metal filling die cavity is the most ideal and the forging forming load is the lowest when using inclined dies and floating dies R uses the rigid plastic finite element method to study the forging forming process of spiral bevel gear. With the help of I-DEAS software, the forming situation of the gear is analyzed and the simulation results are used to guide the die structure design optimization.
Watanabe et al. Designed the tooth profile die according to the meshing characteristics of the driven spiral bevel gear during operation and successfully trial produced the sample parts; kongmei discussed the use of continuous casting and continuous forging process to produce the gear, introduced the advantages of using this process to process the gear blank compared with the traditional process; Yang Shenhua used the numerical simulation technology to verify the use of cold block die forging process to form a car differential The possibility of bevel gear; Kou Shuqing studied the application of cold block die forging technology to the forming process of straight bevel gear; Wang Huajun and others carried out numerical simulation on the precision forging process of driven spiral bevel gear, obtained the workpiece with full tooth shape and reached the conclusion that large section bevel gear is not suitable for cold precision forging; Yang D Y studied the metal flow rule and stress-strain distribution in the rolling process of ring parts; Tian Fuxiang proposed to use the hot precision forging cold extrusion composite forming process to form spur gear, introduced its advantages and designed the corresponding processing equipment; Xia Juchen and others used the method of combination of finite element simulation and process test to apply the cold precision forging process to the gear forming process The effects of die size, blank shape and finishing on the forming process were studied.
Fang Yuan et al. Studied the influence of the gears with different structural and technical parameters on the precision forging process of the driven spiral bevel gear and concluded that the influence of the helix angle and the pressure angle on the forming load of the workpiece is small, and the forming load and the equivalent stress at the root of the tooth are in direct proportion to the module and the number of teeth of the gear; Wang Fengsheng used deform In the software research, the method of first hot precision forging and then machining is used to produce driven spiral bevel gear. By analyzing the metal flow field and the equivalent stress-strain distribution, it is found that the metal flow at the step of the gear boss is difficult. Based on this, the die structure is optimized and the conclusion that the initial forging temperature has little relationship with the energy consumption is obtained.
Yan Hongyan and so on put forward the problems that need to be paid attention to in the process of precision control in the gear processing, and carried out the process test for the planetary gear formed by the hot precision forging cold precision forging composite forming process for the blank with different diameter and different pier diameter ratio, and determined the reasonable process parameters; Cheng mengbiao analyzed the process of the driven spiral bevel gear shaping by the finite element simulation technology, and determined the best one Qiu Dehua, et al. Applied the theory of gear hollow split flow to the forming of straight bevel gear. According to the different amount of cold precision forging at the tooth surface and root, designed two kinds of cold precision forging schemes of standard shape and non-standard shape respectively, and got the conclusion that the non-standard shape is more suitable for the finishing process of straight gear. Zhang Qingping, et al. Used deform The influence of different parameters on the forging process of bevel gear is analyzed by software simulation: improving the die speed is conducive to improving the metal fluidity; compared with cold precision forging, the workpiece and die stress of warm forging process are greatly reduced; the forming load of materials with lower carbon content is smaller, and the life of forming equipment is higher.