This paper investigates the application of gear staggering phase tuning as an effective method to reduce vibrations in spur gear transmissions. The study explores the meshing principles of staggered phase-tuned gears, derives the formula for time-varying meshing stiffness, and establishes the relationship between staggering phase angles and vibration responses. Experimental validation is conducted using a custom-designed test rig, demonstrating significant vibration reduction under optimal phase tuning. Results highlight the potential of this method to enhance gear transmission performance.
1. Introduction
1.1 Background
Vibration and noise in gear systems are critical issues affecting transmission efficiency, durability, and user comfort. Traditional vibration control methods include increasing contact ratio, tooth profile modification, gear shifting, and damping enhancement. However, these approaches often face limitations in adaptability and cost-effectiveness.
1.2 Research Objectives
This study introduces gear staggering phase tuning, a novel method to mitigate vibrations by adjusting the relative angular positions of gear teeth. The objectives are:
- Analyze the meshing principles of staggered phase-tuned gears.
- Derive the time-varying meshing stiffness formula for staggered gears.
- Investigate the relationship between phase angles and vibration responses.
- Validate the method through experimental testing.
2. Gear Staggering Phase Tuning Principles
2.1 Definition and Mechanism
- Staggering Phase Tuning: A gear is divided into multiple segments (e.g., two layers) with a controlled angular offset (staggering phase angle) between them.
- Key Benefit: Alters the meshing timing between gear segments, reducing stiffness fluctuations and vibration excitation.
2.2 Phase Angle Calculation
The relationship between the staggering phase angle (φ) and the gear rotation angle (φ₀) is:\(\varphi = \text{mod}\left(\varphi_0, \frac{2\pi}{z}\right)\) where z is the number of teeth.
2.3 Meshing Behavior
- For standard gears (\(1 < \varepsilon < 2\)), meshing alternates between single-tooth and double-tooth contact.
- Staggered gears can overlap meshing intervals, smoothing contact transitions and reducing stiffness variations.
3. Time-Varying Meshing Stiffness Analysis
3.1 Stiffness Modeling
The total meshing stiffness (\(k_d(t)\)) of staggered gears is the average of two meshing segments:\(k_d(t) = \frac{1}{2}\left[k^{(1)}(t) + k^{(2)}(t)\right]\) where \(k^{(1)}(t)\) and \(k^{(2)}(t)\) are the stiffness functions of the two segments.
3.2 Amplitude Reduction
- The amplitude of stiffness fluctuations depends on the staggering phase angle (p) and contact ratio (ε₀).
- Optimal tuning occurs when \(\varepsilon_0 \approx 2/3\), minimizing stiffness variations (Figure 1).
4. Experimental Setup
4.1 Test Rig Design
A custom test rig was constructed to measure vibrations under different staggering phases. Key components include:
- Servo motor for input drive.
- Load motor for torque application.
- Torque and vibration sensors for data acquisition.
4.2 Sensor Configuration
Sensor Type | Location | Purpose |
---|---|---|
Displacement | Input/output shafts | Measure radial vibrations |
Accelerometer | Gear housing | Monitor acceleration levels |
4.3 Test Parameters
- Input Speed: 500 rpm
- Load Torque: 20 N·m
- Staggering Phases: p = 0, 0.2, 0.4
5. Results and Analysis
5.1 Vibration Displacement
Phase (p) | Input RMS (μm) | Output RMS (μm) | Reduction (%) |
---|---|---|---|
0 | 23.0 | 22.9 | – |
0.2 | 11.8 | 10.3 | 48.7/55.0 |
0.4 | 10.1 | 11.9 | 56.1/48.0 |
5.2 Vibration Acceleration
Phase (p) | Input RMS (m/s²) | Output RMS (m/s²) | Reduction (%) |
---|---|---|---|
0 | 6.89 | 5.85 | – |
0.2 | 5.17 | 4.98 | 24.9/14.9 |
0.4 | 4.22 | 4.08 | 38.8/30.3 |
5.3 Frequency Domain Analysis
- Dominant Frequencies: Rotational frequency (\(f_r\)) and meshing frequency (\(f_m\)).
- Staggering Effect: Reduces amplitudes at \(f_r\) and \(f_m\) (Figure 2).
6. Discussion
6.1 Optimal Phase Angle
- Maximum vibration reduction occurs at p = 0.4 for displacement and p = 0.2 for acceleration.
- This discrepancy is attributed to load distribution and damping effects.
6.2 Load Dependency
- Vibration levels increase with torque, but staggered tuning maintains consistent reduction ratios (Figure 3).
6.3 Comparison with Simulation
- Experimental results align with predictions, validating the theoretical model.
- Discrepancies arise from manufacturing and assembly tolerances.
7. Conclusion
- Gear staggering phase tuning effectively reduces vibrations in spur gear systems.
- Optimal performance depends on contact ratio and phase angle.
- This method offers a cost-effective alternative to traditional vibration control techniques.
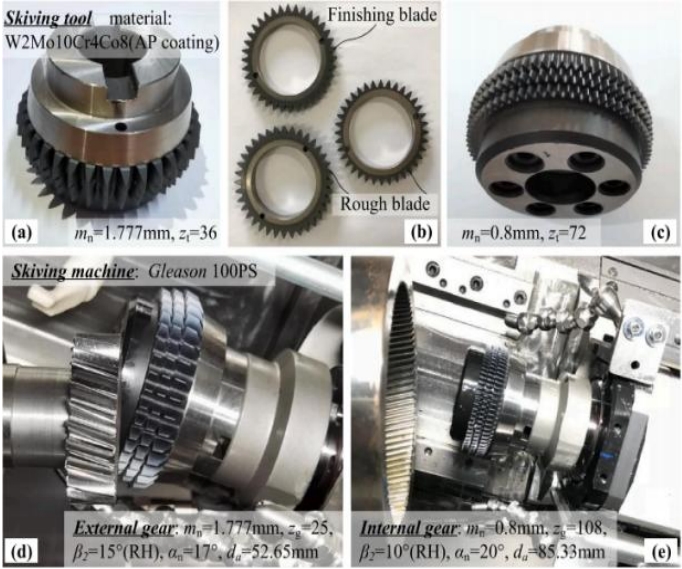