(1) The transmission system of rotating machinery produces torsional vibration when it bears impact load. The main transmission system of rotating machinery can be regarded as a mass spring system composed of several inertia elements. The transmission system will not vibrate when it is loaded stably. At this time, the torque change in the connecting shaft is static and stable, but the transmission system will produce unstable torsional vibration movement under the load disturbance. At this time, the torque on the connecting shaft will change periodically with the rotation angle. The torsional natural frequency of mass spring system is the frequency of periodic change of the connecting shaft. The maximum torque caused by torsional vibration is much larger than that in normal operation. At this time, the stress on the connecting shaft will exceed the allowable strength of the material, resulting in the failure of the mechanical equipment, thus affecting the normal production. This kind of impact vibration has a very serious damage to the mechanical equipment, which makes the transmission system produce fatigue damage, thus reducing the service life of parts.
(2) The vibration of rotating machinery is caused by the periodic change of load. Because of the eccentricity of the rotating parts and the change of the material of the mechanical parts, the periodic change of the load of the transmission system of the rotating machinery often results in the local vibration of the transmission system, which results in the vibration of the whole rotating machinery and finally affects the service life of the mechanical products.
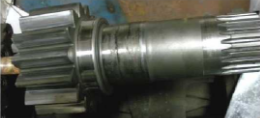
In the gear transmission system of rotating machinery, the fit between the gear shaft and the bearing is generally interference fit. Gear shaft is the key part of rotating machinery to transmit power. It mainly bears alternating load and symmetrical bending stress, which causes fretting on the surface of journal which fits with bearing interference or on the surface of wheel seat which fits with hub interference. Fretting damage mainly occurs on the edge of contact area inside the wheel seat. The fretting of the mating surface causes the damage of the material surface, such as the generation of oxide wear debris, the change of oxide morphology, the plastic deformation of the surface or sub surface or the generation of micro cracks. Under the action of cyclic stress, fretting damage can cause crack growth, which leads to the decrease of fatigue strength or early fracture of components. Fretting damage may occur on the mating surfaces of heat sleeve and press fit, and the interference mating surfaces between the bearing and the bearing seat under large alternating load. In the gear transmission mechanism of complex power equipment, the contact surface between the gear shaft and the bearing is easy to cause fretting wear due to the torsional vibration instability vibration of the transmission system, which leads to the stress concentration source of the parts, increases the vibration stress of the gear journal, expands the fatigue crack on the surface of the metal materials, and causes the fatigue fracture of the gear shaft. In general, the fatigue strength of components will be reduced by 80% after fretting wear. The figure shows the wear and fracture failure of the gear shaft in different rotating mechanical gear transmission systems due to torsional vibration instability.
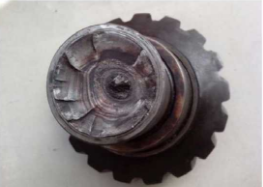
It can be seen from the above reasons for torsional vibration instability of rotating machinery that torsional vibration of rotating machinery causes wear of gear shaft, and wear of gear shaft changes mechanical operation performance, so that torsional vibration instability is intensified, leading to fatigue fracture of gear shaft. Therefore, it is necessary to study the wear phenomenon of the gear transmission of the rotating machinery, so as to put forward the measures to solve the torsional vibration instability and vibration phenomenon of the rotating machinery and reduce the occurrence of production accidents.