The running state of fretting wear is not only related to the yield strength, material rigidity, elastic modulus and elastic-plastic properties of materials, but also closely related to the working parameters such as relative displacement of contact surface, contact load, working frequency, contact mode, surface roughness and cycle period. In addition, fretting wear is also affected by environmental factors such as temperature, pressure, corrosive and radioactive media, which makes it difficult to study fretting wear resistance of materials.
Vingsbo et al. Proposed the concept of fretting diagram, but only described some fretting phenomena, but did not correctly reflect the operation mechanism of fretting wear. Zhou and Vincent established two kinds of fretting pattern theory based on a large number of fretting wear experiments. In essence, the mechanism of fretting wear and the rule of fatigue damage are revealed, and the theory is applied to the study of fretting wear characteristics of different materials.
There are two modes of fretting diagram of material, namely, the fretting diagram of operation condition and the fretting diagram of material response, as shown in the figure. No matter what kind of test conditions, fretting wear always runs in one of the above three areas, so the fretting diagram of the operation conditions with the positive pressure and displacement amplitude as the coordinate axis can be established as shown in the figure. The fretting diagram can be divided into partial slip zone, mixed zone and slip zone by friction, displacement amplitude and cycle number. The formation and size of the mixing zone are mainly related to the characteristics of the friction pair and the medium of the contact interface. There are two main types of fretting damage: fretting wear and fretting fatigue. Fretting wear is mainly characterized by the generation of wear debris, spillage and pockmarks. Fretting fatigue is characterized by crack initiation and crack growth. The fretting diagram corresponding to operation condition is a material response fretting diagram composed of two damage forms, as shown in the figure. The fretting map of material response mainly includes three areas: wear area, crack area and slight damage area.
The division of the three regions mainly depends on different damage types, and the distribution form, shape and size of each damage region are related to the number of cycles. In the wear area, a large number of peeled off debris form more debris accumulation and deeper pits, resulting in serious wear in the contact area; in the crack area, due to the action of large alternating stress, the contact surface produces large elastic deformation and plastic deformation, resulting in the formation of small fatigue cracks on the contact surface, at the same time, the contact surface between the two objects has a cold hardening effect; and the contact surface It is not easy to produce fretting wear in the undamaged area.
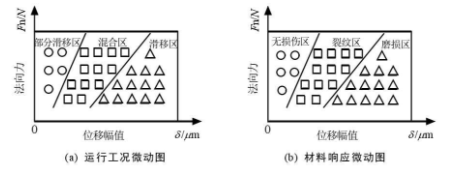
Both fretting wear and fretting fatigue have relative micro motion, the difference is the relative motion of fretting wear The normal movement of N / NF force is imposed by the outside world, and fretting fatigue is caused by the fatigue stress of the material itself. There are two damage mechanisms, fretting wear and fretting fatigue, namely fretting wear on the friction surface and the initiation and propagation of fretting cracks. It can be seen from the fretting diagram of two working conditions: fretting wear of materials is mainly located in the fretting slip area, while it is relatively slight in some slip areas; fatigue cracks first sprout in the mixing area of materials, and then propagate rapidly to some slip areas and slip areas, so the mixing area is the dangerous area for the origin and propagation of fatigue cracks of materials.. It can be seen from the above analysis that the fretting diagram theory provides an important reference for the study of fretting wear mechanism.
In recent decades, fretting wear research has become more and more active, research methods and objects have increased rapidly, and research content is more comprehensive and in-depth. The research methods of elastoplastic mechanics, fracture mechanics, finite element method and energy equation can be used to solve the fretting operation and damage process. The research object of fretting wear has developed from metal materials commonly used in industry to various new composite materials mainly including polymer materials, ceramic materials and powder metallurgy materials. The research environment of fretting wear has developed from general temperature, vacuum and corrosive medium to the harsh environment of special equipment such as ultra-low or ultra-high temperature and strong magnetic field. At present, the research field of fretting wear has developed from the research of fretting wear mechanism to the stage of paying equal attention to the research of fretting wear resistance.