With the development of aerospace, shipbuilding, automotive and other manufacturing industries, the research and application of spiral bevel gears have alsoThe spiral bevel gear has been gradually gaining widespread attention for its compact structure, strong load capacity, and high degree of coincidence.Currently, the commonly used material for spiral bevel gears is 20CrMnTi,Due to its high hardness, strong chemical reactivity, and poor heat dissipation, the machinability of end-milling spiral bevel gears is relativelyPoor, high cutting forces and high cutting temperatures can easily lead to severe tool wear and poor workpiece processing qualityand low processing efficiency, which seriously affects the cutting efficiency and tool life. In the process of machining spiral bevel gears,In the process of machining, reasonable cutting parameters can not only improve the tool life and workpiece surface roughness, but also improve the machining efficiency.The cutting parameters of end milling spiral bevel gears are optimized using RBF neural network-NSGA genetic algorithm.explore cutting schemes that minimize tool wear and optimize workpiece surface roughness.Firstly, analyze the milling principle of generating spiral bevel gears based on the generating method, and determine the cutting position relationship.Department: Analyzing the structure of spiral bevel gears, deriving the equations for cutting concave and convex tooth surfaces, and building a cutting tooth surface modelObtain the mathematical equation of the cutting trajectory of the tool, discuss the motion trajectory and wear pattern of the machining tool, and establishEstablish a mathematical model for tool wear; visualize the mathematical model of tool wear using Matlab softwareAnalyze the influence of cutting parameters on tool wear; explore the relationship between the residual height of the machined workpiece surface and the cutting parameters.and establish a mathematical model of surface roughness, providing a theoretical basis for the subsequent research on surface roughness of spiral bevel gears.Theoretical basis.Secondly, the simulation analysis of the cutting process and cutting tool of the spiral bevel gear under high-speed dry cutting conditions was conducted.CATIA software is used to establish three-dimensional models of spiral bevel gears and cutting tools, and throughDEFROM simulation software conducts simulation analysis on end milling spiral bevel gears to explore the cutting process.The variation laws of force and cutting temperature; explore the wear forms, mechanisms, and processed workpieces of the cutting tool during the cutting processThe variation law of the surface deformation of the workpiece can reflect the actual roughness of the processed workpiece surface.The roughness provides technical support for experimental research on end milling spiral bevel gears under high-speed dry cutting conditions.
Furthermore, cutting experiments were conducted on the spiral bevel gear using end-face milling. The ultra-depth display technology was used toThe tool wear is detected by using microscopes, scanning electron microscopes, and energy spectrometers to analyze the tool wear under different cutting parameters.The wear patterns and wear mechanisms of cutting tools, and explore the changing rules of tool wear under different cutting parameters; use the P40 rolling inspection machine to detect the surface roughness of the workpiece, and explore the influence of different cutting parameters on the spiral bevel gearThe variation law of the roughness of the processed surface.Finally, based on the experimental results, the NSGA-II genetic algorithm with RBF neural network approximation model was adopted.The cutting parameters of spiral bevel gears are optimized by using feed rate and cutting speed as inputs, and selecting the toolMinimal wear, minimal surface roughness, and maximum processing efficiency are used as outputs to obtain a multi-objective ParetoThe frontier diagram and the mutual influence relationship between different targets are explored to determine the optimal cutting parameters.
In mechanical transmission systems, gear transmissions have high efficiency and large torque, and spiral bevel gears are a special type of conical gearGears are divided into tapered tooth spiral bevel gears and constant tooth spiral bevel gears according to the type of tooth, which have overlappingThe advantages of large coefficient, smooth transmission and low noise. Compared with belt drive and chain drive, the spiral bevel gear has the advantages of high transmission efficiency, high reliability, and low noise.It is characterized by high efficiency, strong carrying capacity, wear resistance, and long service life, and is mainly used in automotive and aerospace industries.The domain is shown as the helicopter tail rotor drive system and the automotive transmission system. Spiral bevel gearThe position and shape of the tooth contact area in the transmission are important references for evaluating the transmission accuracy and performance of meshing gear pairsTherefore, it is necessary to conduct focused research and analysis on the cutting process of spiral bevel gears.
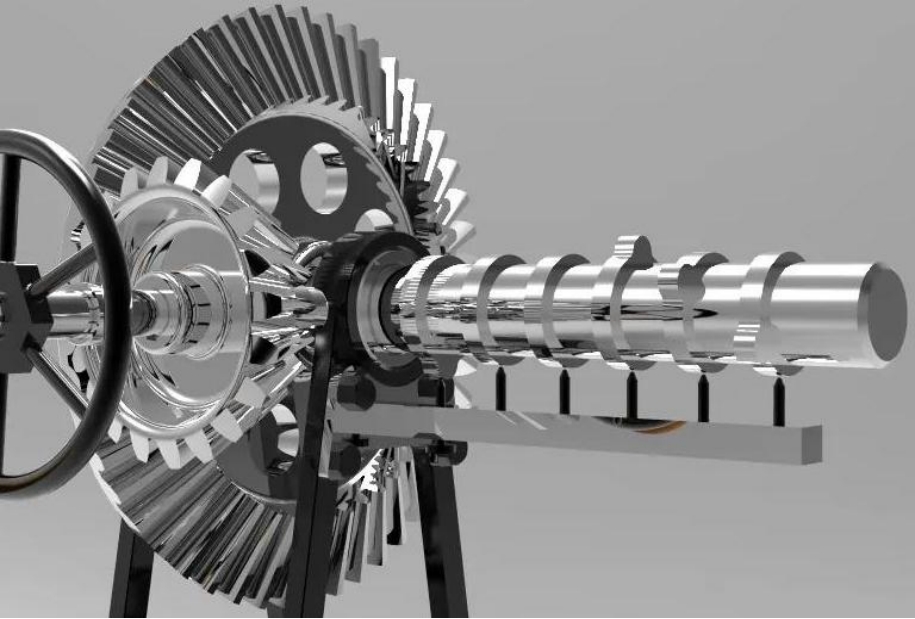
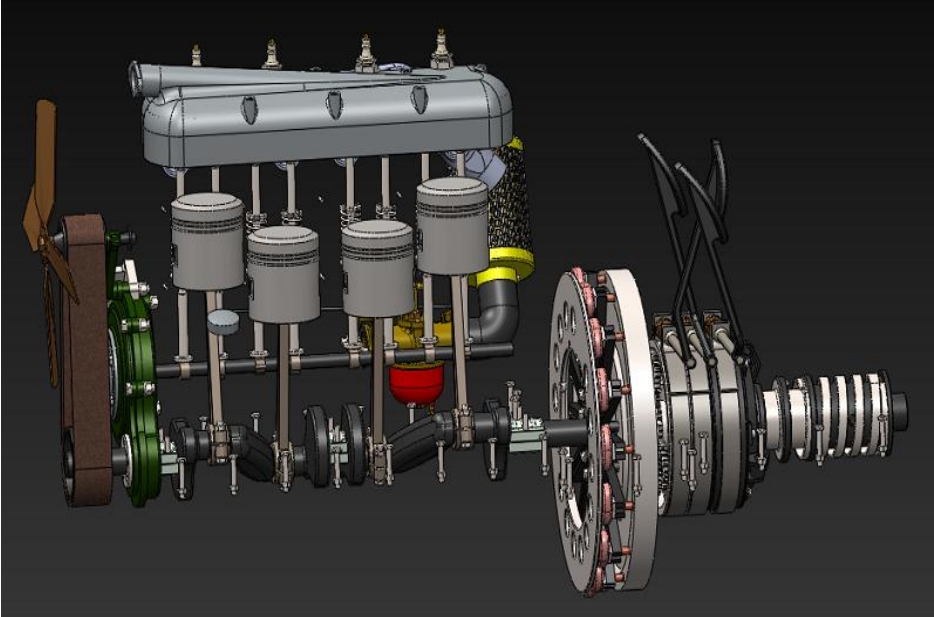
Domestic spiral bevel gears are mainly processed using traditional single and double-sided inner and outer knives, as shown in process the cutter head of the spiral bevel gear, shows the cutting tool for processing the spiral bevel gear. The cutting tool isWear is a common phenomenon, mainly related to the mechanical properties of the tool and workpiece materials, cuttingIt is related to cutting parameters, cooling conditions, cutting force, and cutting temperature. Physical impact and chemical reaction work togetherIt is the main cause of tool wear, and the selection of cutting parameters during the machining process can affect the actual arc tooth profile.surface quality of bevel gears, therefore studying the influence of cutting parameters on tool wear and surface roughness of the processed workpiece.The influence law is necessary; taking the minimum tool wear and minimum surface roughness as the main indicators, throughThe RBF neural network algorithm and NSGA-II optimization genetic algorithm are used to optimize cutting parameters, based on the actualThe processing requirements require the reasonable selection of cutting parameters.
Pass throughUsing finite element simulation and experimental verification, analyze the cutting parameters of end milling spiral bevel gearsThe wear of the lower cutting tool and the change rule of the stress and strain on the surface of the workpiece; explore the wear mode, mechanism, andThe surface roughness of the processed workpiece is minimized using a RBF neural network NSGA-II genetic algorithm to minimize tool wear.The optimization objective is to minimize the cutting loss, the minimum workpiece surface roughness, and the maximum processing efficiency, achieving optimal cutting parameters.and provide technical support for the cutting process of spiral bevel gears.
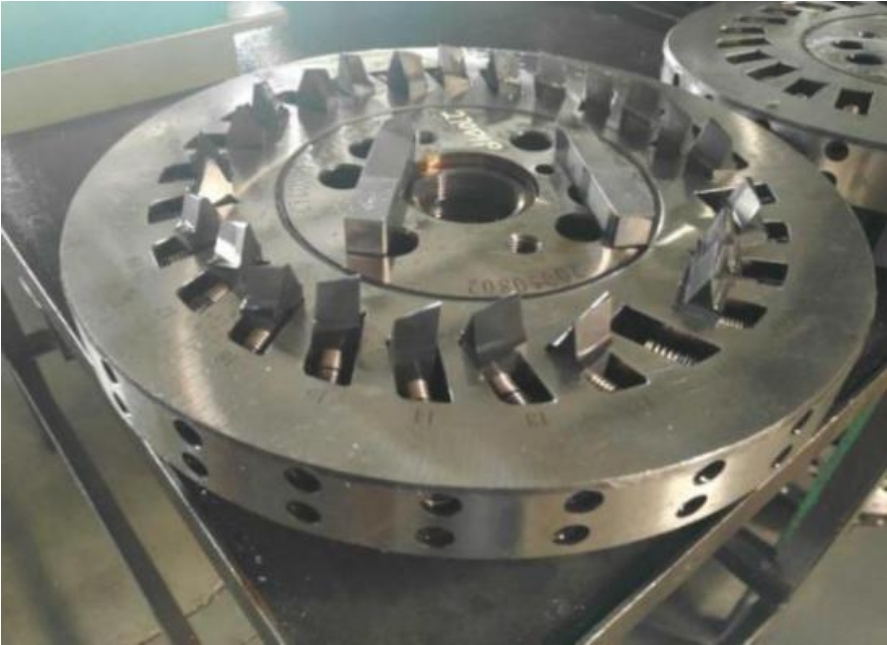
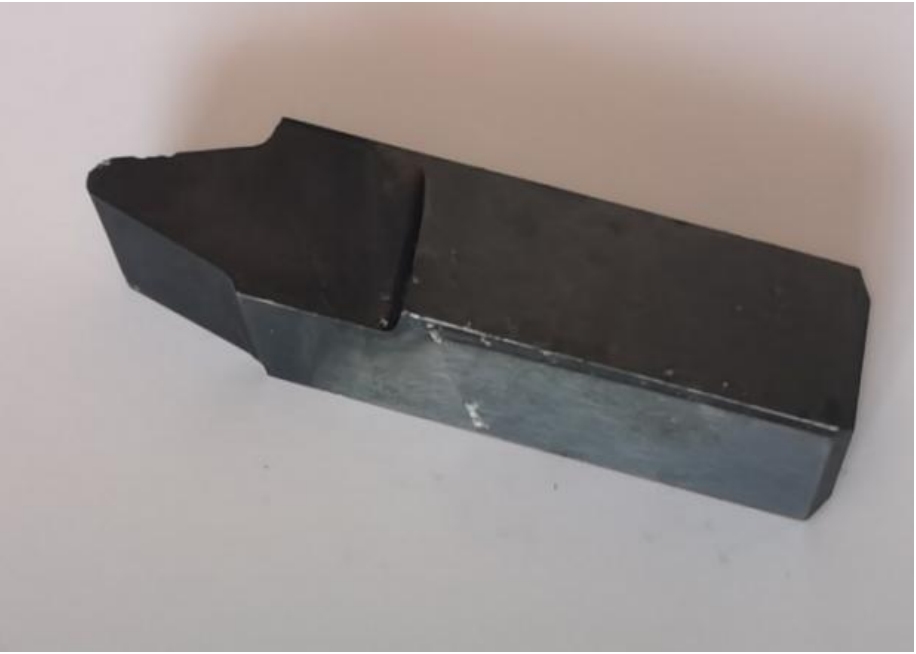
Mathematical expressions for the cutting edge, rake angle, and clearance angle of the spiral bevel gear milling cutter are proposed by reducing the rake angle and clearance angle of the tool.A new method for improving the wear characteristics of cutting tools by using a gradient design method. A design method for surface milling arc-tooth conicalA new method for gear transmission, which optimizes the boundary constraints by defining the desired topography of the pinion’s active surfaceThe algorithm reduces the transmission noise and vibration level of face milling spiral bevel gears. A method based on cutting toolThe tooth surface correction method with blade correction, which not only effectively avoids tooth edge contact, but also reduces tooth surfaceMaximum contact stress, reducing the adverse effects of misalignment. Proposed a high-order transmission errorand study the nonlinear vibration during the process of cutting spiral bevel gears to reduce the machining errors.The difference in the influence law of the method compared to the parabolic transmission error method is that the maximum transmission error of the high-order transmission error method isThe root mean square of the time response has been reduced by 44%, and the peak transmission error has been reduced throughout the entire frequency range.35%. To solve the problem that the geometric meshing theory is not applicable to calculating the area where the point cannot cover the entire tooth surfaceIn extreme cases, a new adaptive geometric meshing theory is proposed. A method is proposed that includesThe dynamic model of flexible links such as shafts and bearings is established using the multi-harmonic balance method combined with continuous-time Fourier transform.Instead, a nonlinear algebraic equation set is established from the obtained nonlinear differential equation of motion, thereby improving the accuracy of the arcThe machining accuracy of the bevel gear. Proved that precision plastic forming technology can manufacture arc bevel gearThe numerical analysis model of the wheel is reliable. For the current simulation software, the generation of arcs in face millingThe discrete curves of bevel gears are often too non-isometric to directly generate 3D models and mesh models.propose a new global optimization algorithm, namely Real-coded Relaxed Genetic Algorithm (RRGA), andThe effectiveness of the algorithm was verified through experiments.
The main factors affecting the quality of the machined surface of the spiral bevel gear include cutting force, cutting heat, cutting parameters, and cutting tools.Due to the interaction of the above factors in the actual processing process, it is currently only possible to control the residual stress throughThe degree of influence of surface roughness is obtained by varying the factors that affect the preparation process. For different mechanical processing processes, multiple mathematical models of roughness are established to verify the relationship between the surface roughness of the processed surface and the cutting parameters.In order to improve the quality of the machined surface of the spiral bevel gear, according to the forming process of the spiral bevel gear,The principle and meshing theory were analyzed through 3D modeling and finite element simulation software.Using CNC milling to process spiral bevel gears, ensuring high surface processing quality. For ballIn the process of head milling, there are common problems such as small cutting band width and poor surface quality. A concave head disc milling cutter is proposedThe face milling method not only improves the surface processing quality of the spiral bevel gear, but also increases production efficiency.Efficiency. Based on the fact that the tooth surface is formed by the intersection points of the tool edge and the specific sequence within a specific tool cycle.Based on the theoretical study, numerical simulation and experimental research, the relationship between design parameters and process parameters on the development of the tooth profile of arc-tooth gear is revealed.The influence law of the surface roughness distribution of bevel gears. Using coated carbide tool for semi-finishingHard tool steel for machining or finishing, the results show that if a smaller surface roughness is obtained, higher cutting speeds should be used.Cutting at a high speed and with a small back feed. Analyzing at different milling speedsTC4 surface morphology, it is found that the machined surface will decrease first and then increase with the increase of cutting speedResearch shows that the surface quality of the tool will rapidly decrease after wear, and the wear is mainly concentrated on the cutting edge.Through the experimental research on turning different hardness GCr15 workpieces with PCBN tools,The minimum surface roughness of the workpiece is around HRC50, and below HRC50, the roughness increases with the increase of hardness.Increase it.
In summary, scholars at home and abroad mainly start from theoretical models, through cutting force, cutting heat andThe research on the surface quality of spiral bevel gear milling machining is conducted based on the tool structure, but the optimization algorithm for parameters is not considered.There are few documents on the surface quality of high-arc bevel gear machining, so it is necessary to obtain the optimal cutting parameters through optimization algorithms.The surface roughness is obtained by using the residual height of the processed workpiece surface, which optimizes the surface roughness whileand production efficiency can be improved.
Research on the wear form, mechanism, and surface roughness of machined workpieces of spiral bevel gear toolsResearch, starting from the theory of spiral bevel gear forming and meshing principle, to establish the relationship between tool wear and workpiece surface roughnessStudy the model, analyze the wear pattern of the tool and the variation law of the surface strain of the processed workpiece through simulation, and summarizeThe cutting experiments explore the wear pattern, mechanism, and surface roughness change law of the tool;Taking tool wear, minimum workpiece surface roughness, and maximum processing efficiency as the main evaluation indicators, RBFThe neural network NSGA-II multi-objective optimization algorithm is used to optimize cutting parameters.(1) Analyze the principle of milling gears based on the generating method for machining spiral bevel gears, and clarify the cutting trajectory of the toolTheoretical derivation of the accuracy of the concave and convex tooth surfaces of the spiral bevel gear is carried out by analyzing the cutting trajectory of the tool.Analyze and obtain the wear model of the tool during the cutting process; analyze the machined surface of the spiral bevel gear to obtain the surface roughnessThe mathematical model of the surface residual height provides a theoretical basis for subsequent models of the surface roughness of the processed surface.(2) Conduct finite element simulation analysis on end face milling spiral bevel gears. Through CATIA software,Build corresponding simulation models for the cutting tool and the workpiece being processed, and use DEFORM simulation software to simulate high-speedUnder dry cutting conditions, the variation laws of tool wear and the surface strain of the processed workpiece under different cutting parameters;The change in surface strain of the workpiece can reflect the variation law of the surface roughness of the actual spiral bevel gear, and explore the cutting process.The wear pattern and mechanism of the tool during the process, as well as the variation of the surface roughness of the processed workpiece, provide a theoretical basis for high-speed end milling.The experimental study of spiral bevel gears provides corresponding theoretical guidance.(3) Cutting experiments on spiral bevel gears were conducted using end milling. Ultra-depth visualization was used to achieve high accuracy and precision.Microscope, scanning electron microscope and energy spectrometer are used to detect tool wear and analyze the effect of different cutting parameters on tool wear.The wear form and wear mechanism of cutting tools, and explore the variation law of tool wear under different cutting parameters;The P40 roll inspection machine detects the residual height of the workpiece surface and explores the characteristics of the spiral bevel gear under different cutting parameters.The variation law of the surface roughness of the machined wheel.(4) The NSGA-II genetic algorithm using the RBF neural network approximation model is used to optimize the cutting parameters of the spiral bevel gear.Select feed rate and cutting speed as inputs, and minimize tool wear, surface roughness, and cutting time.
Spiral bevel gears have complex curved surface structures, and accurate machining can be achieved through reasonable cutting trajectories and tooth surface profiles.The mathematical model of tool wear and surface roughness of 12Cr1MoV steel is developed.The variation law of surface roughness of parts is discussed in this chapter, starting from the meshing theory of spiral bevel gears and the principle of milling, and focusing on the cutting process.Based on the trajectory and machined surface model, establish an accurate tool wear model and residual surface of the machined surfaceThe height model is created and visualized, and the main influencing factors are analyzed to facilitate subsequent finite element simulationand provide necessary conditions for experimental research.