With the development of mechanical industry, the importance of transmission system is more and more reflected. As the main part of transmission system, gear plays a very important role in machinery related industries. In many cases, there are higher requirements for the transmission accuracy and stability of gears.
Ordinary spiral bevel gears and hypoid gears are widely used. The advantages of ordinary spiral bevel gears are as follows: large overlap coefficient, high strength, high reliability, good wear resistance and high transmission efficiency. They are widely used in aircraft, ships, machine tools, heavy industry and other mechanical products.
Hypoid gear is essentially a kind of spiral bevel gear. The most important difference between the two is that the hypoid gear has an offset, that is, staggered shaft transmission. The so-called offset refers to the length of the common vertical line between the two rotation axes of the gear transmission, that is, the shortest distance. If the offset is set to zero, it is a common bevel gear. The figure 1 shows a pair of meshing hypoid gears.
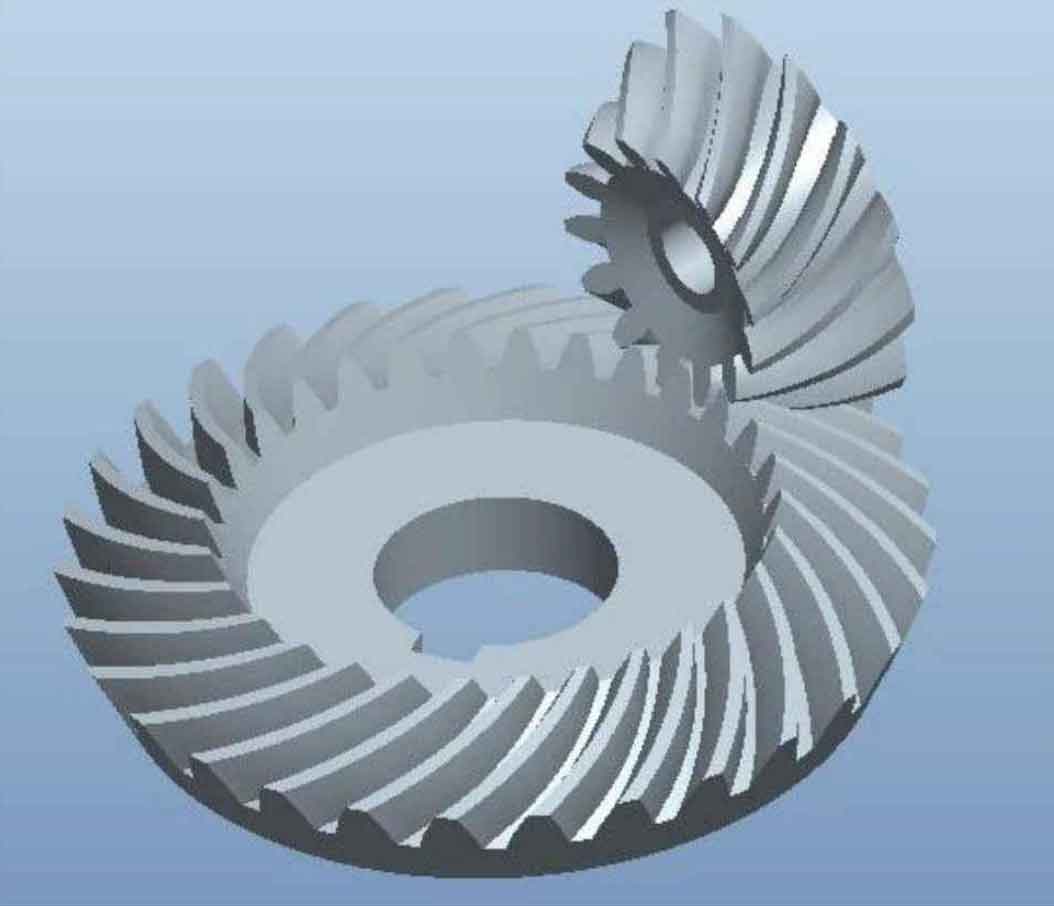
Under the condition of meeting the requirements of transmission ratio and large wheel diameter, the small wheel diameter of hypoid gear is larger than that of bevel gear in the same case, so that the small wheel can obtain greater stiffness and strength; The helix angle of the big wheel is different from that of the small wheel. The large helix angle of the small wheel increases the overlap coefficient of the gear and makes the transmission process more stable; The rotation axis of the quasi bicurface small wheel can be offset up and down, which can be used to raise or lower the vehicle body on the rear axle of the automobile.
The tooth surface of hypoid gear is complex, and the manufacturing process of hypoid gear is more complex and cumbersome. In the manufacturing process, special machine tools need to be used, and the processing parameters should be set reasonably, and repeated calculation iterations and tooth dressing should be carried out. For example, the Gleason hypoid gear processing machine tool used by many enterprises is shown in the figure 2.
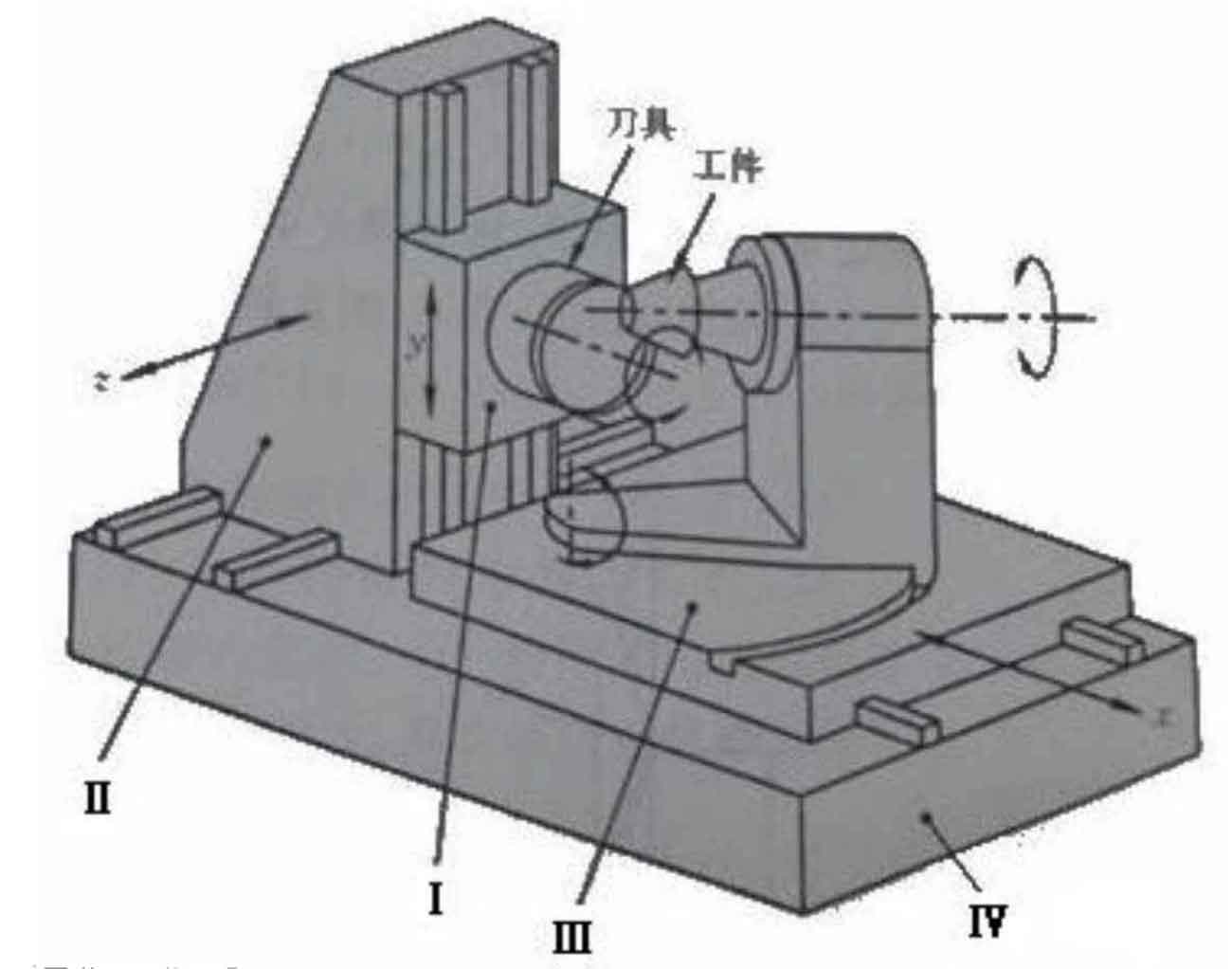
The machine tool has six movements: three rotary movements and three linear movements. Where I is the offset adjusting rod of hypoid gear, II is the cutter head column, III is the rotary table used to adjust the included angle between the workpiece and the cutter axis, and IV is the machine base. In the process of machining hypoid gears, in addition to the rotation of the workpiece, it is necessary to complete the machining through other five-axis related movements, which leads to the complexity of the machining process.