In the process of helical gear meshing, because the hardness of the gear shaft is higher than that of the driven gear, the maximum meshing stress usually occurs on the driven wheel. According to the meshing characteristics of helical gears, the maximum contact stress usually corresponds to the maximum root bending stress, and the tooth profile modification of driven gear is also needed. Therefore, the contact stress results on the driven gear are extracted. The diagram shows the time domain diagram of the maximum contact stress of the driven wheel without modification.
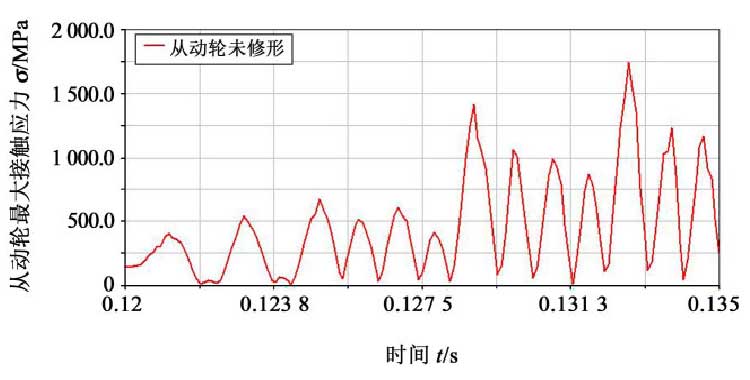
It can be seen that the maximum contact stress of 1746.6 MPa occurs at 0.1327 s, which is located at the end of the gear, where the tooth top of the driven gear is engaged with the root of the driving gear, which is easy to cause the phenomenon of “end meshing”; from the figure, the contact stress is constantly changing during the meshing process, and the instantaneous value at the wave crest is large, and the average contact stress is 449.3 MPa. From the transient dynamic analysis, it can be concluded that the backlash increases the impact of meshing, which makes the contact stress relatively large and exceeds the allowable stress. The peak value of the contact stress can be reduced by using appropriate profile modification.