Introduction
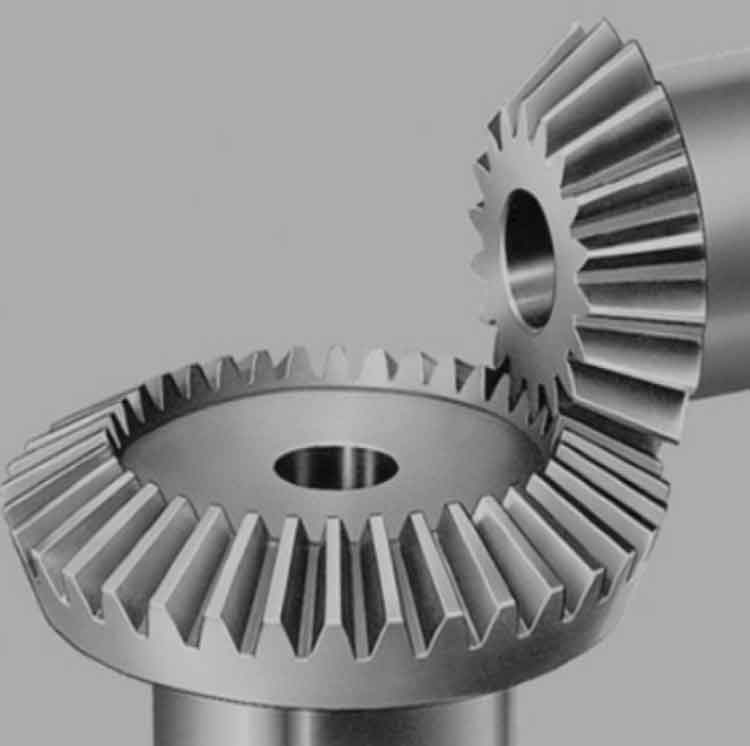
Straight bevel gear is pivotal in various mechanical systems, ensuring efficient power transmission between intersecting shafts. Due to their crucial role, monitoring the wear and tear of these straight bevel gear is essential to prevent failures and maintain optimal performance. This article delves into the wear detection and monitoring techniques for straight bevel gear mechanisms, highlighting the importance, methods, and benefits of each approach.
Importance of Wear Detection and Monitoring
- Preventive Maintenance:
- Early detection of wear allows for timely interventions, preventing catastrophic failures.
- Cost Efficiency:
- Minimizes unexpected downtime, thus reducing maintenance and replacement costs.
- Enhanced Safety:
- Ensures the safe operation of machinery by avoiding sudden straight bevel gear failures.
- Performance Optimization:
- Maintains the optimal performance of straight bevel gear mechanisms by monitoring their condition regularly.
Common Types of Wear in Straight Bevel Gear
- Abrasive Wear:
- Caused by hard particles that grind against the straight bevel gear teeth.
- Adhesive Wear:
- Occurs when material transfers from one straight bevel gear tooth to another due to friction.
- Fatigue Wear:
- Results from repeated loading, leading to cracks and eventual tooth breakage.
- Corrosive Wear:
- Caused by chemical reactions between the straight bevel gear material and environmental factors.
Wear Detection Techniques
1. Visual Inspection
Method:
- Regularly inspecting straight bevel gear visually for signs of wear, such as pitting, scoring, or cracks.
Advantages:
- Simple and cost-effective.
- Requires minimal equipment.
Disadvantages:
- Subjective and dependent on the inspector’s experience.
- Limited to surface wear and may not detect subsurface issues.
Checklist for Visual Inspection:
- Look for visible cracks or fractures.
- Check for pitting or scoring on straight bevel gear teeth.
- Examine the overall condition of the v surface.
2. Vibration Analysis
Method:
- Monitoring the vibration patterns of straight bevel gear mechanisms using accelerometers.
Advantages:
- Effective for early detection of wear and misalignment.
- Can identify specific types of wear through vibration signatures.
Disadvantages:
- Requires specialized equipment and expertise.
- Can be influenced by external vibrations and noise.
Table 1: Vibration Analysis Parameters
Parameter | Normal Range | Wear Indication |
---|---|---|
Acceleration (g) | 0-1 g | > 1 g |
Velocity (mm/s) | 0-10 mm/s | > 10 mm/s |
Displacement (µm) | 0-50 µm | > 50 µm |
3. Oil Analysis
Method:
- Analyzing the lubricant oil for the presence of wear particles.
Advantages:
- Can detect wear before it becomes visually apparent.
- Provides information on the type of wear and potential sources.
Disadvantages:
- Requires regular sampling and laboratory analysis.
- May not provide real-time data.
Table 2: Oil Analysis Indicators
Indicator | Normal Range | Wear Indication |
---|---|---|
Metal Particles (ppm) | 0-50 ppm | > 50 ppm |
Viscosity (cSt) | Within spec | Deviation from spec |
Water Content (%) | 0-0.1% | > 0.1% |
4. Acoustic Emission Analysis
Method:
- Using sensors to detect high-frequency sound waves generated by straight bevel gear wear.
Advantages:
- Highly sensitive to early stages of wear.
- Can detect microscopic cracks and surface defects.
Disadvantages:
- Requires specialized sensors and data analysis tools.
- Can be affected by background noise.
Checklist for Acoustic Emission Analysis:
- Calibrate sensors properly before use.
- Position sensors to capture sound waves accurately.
- Analyze data for high-frequency emission patterns indicative of wear.
5. Thermography
Method:
- Using infrared cameras to monitor the temperature distribution on straight bevel gear surfaces.
Advantages:
- Non-invasive and provides real-time data.
- Can identify hotspots indicative of excessive friction or wear.
Disadvantages:
- Requires specialized equipment.
- Temperature variations can be caused by factors other than wear.
Monitoring Techniques
1. Continuous Online Monitoring
Method:
- Installing sensors and monitoring systems for real-time data collection and analysis.
Advantages:
- Provides continuous monitoring and early detection of wear.
- Allows for predictive maintenance strategies.
Disadvantages:
- High initial cost for installation and setup.
- Requires integration with existing systems and data management infrastructure.
Checklist for Continuous Online Monitoring:
- Ensure proper installation of sensors.
- Regularly calibrate and maintain monitoring equipment.
- Analyze data in real-time for immediate wear detection.
2. Periodic Offline Monitoring
Method:
- Conducting scheduled inspections and measurements at regular intervals.
Advantages:
- Lower cost compared to continuous monitoring.
- Suitable for less critical applications.
Disadvantages:
- Potential for wear to progress between inspections.
- May miss sudden or unexpected wear events.
Table 3: Comparison of Monitoring Techniques
Technique | Frequency | Cost | Sensitivity | Suitable Applications |
---|---|---|---|---|
Continuous Online | Real-time | High | High | Critical machinery |
Periodic Offline | Scheduled | Moderate | Moderate | Non-critical machinery |
Implementing Wear Detection and Monitoring Systems
- Assessment of Needs:
- Evaluate the criticality of the straight bevel gear mechanism and determine the appropriate level of monitoring required.
- Selection of Techniques:
- Choose the most suitable wear detection and monitoring techniques based on the application and budget.
- Installation and Calibration:
- Install sensors and monitoring equipment, ensuring proper calibration for accurate data collection.
- Data Analysis and Interpretation:
- Use specialized software and expertise to analyze the collected data and identify wear patterns.
- Maintenance Planning:
- Develop maintenance schedules and plans based on the detected wear and predicted straight bevel gear lifespan.
Case Study: Wear Monitoring in a Manufacturing Plant
Background:
- A manufacturing plant experienced frequent straight bevel gear failures in their conveyor systems, leading to costly downtime.
Solution:
- Implemented a comprehensive wear monitoring system using vibration analysis and oil analysis.
Results:
- Early detection of wear allowed for timely maintenance, reducing unexpected failures.
- Improved straight bevel gear lifespan and overall reliability of the conveyor systems.
Table 4: Case Study Results
Parameter | Before Monitoring | After Monitoring |
---|---|---|
Unexpected Downtime (hrs) | 60 hrs/month | 15 hrs/month |
Gear Lifespan (months) | 8 months | 16 months |
Maintenance Costs ($) | $60,000/year | $35,000/year |
Conclusion
Effective wear detection and monitoring techniques are crucial for maintaining the performance and longevity of straight bevel gear mechanisms. By employing a combination of visual inspection, vibration analysis, oil analysis, acoustic emission analysis, and thermography, industries can ensure early detection of wear and implement timely maintenance strategies. Continuous online monitoring offers real-time data for critical applications, while periodic offline monitoring provides a cost-effective solution for less critical machinery. Implementing these techniques not only enhances gear reliability but also contributes to significant cost savings and improved operational efficiency.