1. Introduction
Wind energy has emerged as a crucial renewable energy source in the global pursuit of sustainable power generation. Wind turbines, with their ability to convert the kinetic energy of the wind into electrical energy, play a central role in this transition. The gearbox is a vital component within the wind turbine system, serving as the mechanical heart that transmits and converts the rotational speed and torque. However, the gearbox is also prone to various forms of damage, which can significantly impact the performance and reliability of the entire wind turbine. This article focuses on the in-depth analysis of gear damage in wind turbine gearboxes, with a particular emphasis on the causes and preventive measures.
2. Structure and Function of Wind Turbine Gearboxes
(1) Gearbox Configuration
Wind turbine gearboxes typically employ a complex arrangement of gears to achieve the desired speed increase. The most common configuration is the planetary gear system, which consists of a sun gear at the center, surrounded by multiple planetary gears that mesh with both the sun gear and an outer ring gear. This design allows for efficient power transmission and torque multiplication while maintaining a compact size. A schematic diagram of a typical wind turbine gearbox is shown in Figure 1.
[Insert Figure 1: Schematic Diagram of Wind Turbine Gearbox]
(2) Gearbox Function
The primary function of the gearbox is to increase the relatively low rotational speed of the wind turbine rotor to a higher speed suitable for driving the generator. This speed increase is essential to match the generator’s operating requirements and optimize power generation efficiency. Additionally, the gearbox must be able to handle the significant torque generated by the rotor, ensuring smooth and reliable power transfer.
3. Common Gear Damage Modes in Wind Turbine Gearboxes
(1) Pitting
Pitting is a surface fatigue damage mode that appears as small pits or craters on the gear tooth surface. It is caused by the repeated application of high contact stresses, which leads to the initiation and propagation of microcracks. Over time, these microcracks coalesce, resulting in the formation of pits. Pitting can significantly reduce the surface quality of the gear teeth, leading to increased vibration, noise, and ultimately, a decrease in gearbox performance.
(2) Spalling
Spalling is a more severe form of surface damage compared to pitting. It involves the detachment of relatively large pieces of material from the gear tooth surface. Spalling can occur due to a combination of factors, including high contact stresses, poor material quality, and improper heat treatment. The presence of spalling not only affects the gear’s ability to transmit power smoothly but also poses a significant risk of further damage to other components within the gearbox.
(3) Tooth Breakage
Tooth breakage is a catastrophic failure mode that can lead to immediate shutdown of the wind turbine. It can occur as a result of excessive bending stresses, which may be caused by overloads, impact loads, or fatigue. Tooth breakage can also be attributed to manufacturing defects, such as cracks or voids in the gear material, or improper heat treatment that results in brittle gear teeth.
4. Analysis of Gear Damage Causes
(1) Material Factors
The quality of the gear material plays a crucial role in determining its resistance to damage. In the case of wind turbine gears, alloy steels such as 18CrNiMo7 – 6 are commonly used due to their high strength and toughness. However, if the material does not meet the required specifications, it can be more susceptible to damage. For example, impurities or inclusions in the material can act as stress concentrators, facilitating the initiation of cracks. Table 1 summarizes the typical chemical composition requirements for 18CrNiMo7 – 6 steel used in wind turbine gears.
Element | Composition Range (%) |
---|---|
C | 0.15 – 0.21 |
Si | ≤ 0.40 |
Mn | 0.50 – 0.90 |
P | ≤ 0.015 |
S | ≤ 0.010 |
Cr | 1.50 – 1.80 |
Ni | 1.40 – 1.70 |
Mo | 0.25 – 0.35 |
Al | 0.02 – 0.05 |
Cu | ≤ 0.20 |
(2) Manufacturing Process Defects
- Forging Defects
The forging process is used to shape the gear blank and improve its mechanical properties. However, improper forging techniques can introduce defects such as cracks, porosity, and non-uniform grain structure. These defects can reduce the material’s strength and fatigue resistance, making the gear more prone to damage during operation. - Machining Errors
During the machining process, inaccuracies in gear tooth profile, surface finish, and dimensional tolerances can occur. These machining errors can lead to uneven load distribution on the gear teeth, resulting in increased contact stresses and accelerated wear. For example, if the tooth profile is not accurately machined, it can cause improper meshing between gears, leading to excessive wear and the potential for pitting and spalling. - Heat Treatment Problems
Heat treatment is a critical step in enhancing the mechanical properties of gears. Improper heat treatment can result in issues such as incorrect hardness levels, non-uniform microstructure, and excessive residual stresses. For instance, if the quenching process is not properly controlled, it can lead to the formation of hard and brittle martensite, which is more prone to cracking. Table 2 shows the typical heat treatment requirements and resulting microstructure and hardness values for wind turbine gears.
Heat Treatment Process | Microstructure | Hardness (HRC) |
---|---|---|
Carburizing | Surface: High carbon martensite + retained austenite; Core: Low carbon martensite + ferrite + pearlite | Surface: 58 – 62; Core: 35 – 45 |
Quenching and Tempering | Fine tempered martensite + carbide | Appropriate hardness range depending on application |
(3) Operating Conditions and Loads
- Overloading
Wind turbines are often subjected to variable wind conditions, which can result in sudden increases in torque and overloads on the gearbox. Overloading can cause the gear teeth to experience stresses beyond their design limits, leading to premature failure. For example, during strong gusts of wind, the rotor can transmit a much higher torque to the gearbox than under normal operating conditions. - Variable Loading and Fatigue
The cyclic nature of wind loads causes the gears to experience repeated loading and unloading, which can lead to fatigue damage. Fatigue cracks can initiate at stress concentration points, such as the root of the gear teeth, and gradually propagate over time. The combination of variable loading and fatigue is a significant contributor to the development of pitting and spalling on the gear surfaces. - Lubrication Failure
Proper lubrication is essential for reducing friction and wear between gear teeth. If the lubrication system fails, either due to a lack of lubricant, contamination, or improper lubricant viscosity, it can lead to increased friction and heat generation. This can cause the gear teeth to overheat, leading to surface damage and a reduction in gear life. In addition, lubricant contamination with particles or moisture can act as abrasives, accelerating wear on the gear surfaces.
(4) Environmental Factors
- Corrosion
Wind turbines are exposed to harsh environmental conditions, including moisture, salt spray (in coastal areas), and temperature variations. These environmental factors can cause corrosion of the gear surfaces, which can weaken the material and promote the initiation of cracks. Corrosion can also lead to pitting and surface roughening, further exacerbating wear and damage. - Temperature Extremes
Both high and low temperatures can have a significant impact on the performance of wind turbine gearboxes. High temperatures can cause the lubricant to degrade, reducing its effectiveness and increasing the risk of lubrication failure. Additionally, thermal expansion and contraction of the gear components can lead to misalignment and increased stresses. Low temperatures, on the other hand, can cause the lubricant to thicken, increasing the resistance to motion and potentially leading to cold start problems and excessive wear.
5. Case Study: Analysis of a Specific Gear Damage Incident
(1) Incident Description
A particular model of wind turbine experienced a significant gearbox failure after approximately 8 months of operation. Vibration monitoring detected abnormal behavior, and subsequent inspections using an endoscope and dismantling of the gearbox revealed severe spalling on the teeth of the third – stage planetary gear. The other gears in the gearbox, including the third – stage sun gear and ring gear, showed only minor wear.
(2) Inspection and Analysis Results
- Macroscopic Observation
Visual inspection of the gearbox and the damaged planetary gear confirmed the presence of extensive spalling on one of the teeth of the third – stage planetary gear. The remaining teeth of the three other planetary gears in the same stage exhibited only wear. The sun gear and ring gear in contact with the planetary gears showed minor wear marks. Based on the damage patterns and the meshing relationships between the gears, it was determined that the spalling of the planetary gear was the initial failure, which then led to the wear of the other gears. - Chemical Composition Analysis
Samples were taken from the damaged planetary gear and analyzed for chemical composition using inductively coupled plasma optical emission spectrometry (ICP – OES) according to the standard GB/T 20125 – 2006. The results indicated that the chemical composition of the gear material met the requirements of EN 10084 – 2008 for 18CrNiMo7 – 6 steel, ruling out material composition as a cause of the failure. - Metallographic Examination
Metallographic samples were prepared and analyzed for microstructure and non – metallic inclusions. The non – metallic inclusions were found to be within the acceptable limits. However, the microstructure analysis revealed several issues. The tooth surface hardness, measured at 57.5 HRC on the left side and 57.4 HRC on the right side, was lower than the required range of 58 – 62 HRC. The internal oxidation depth was measured at 2.45 mm on the left side and 2.58 mm on the right side, which exceeded the allowable limit. The martensite and residual austenite levels at the tooth root were also not in accordance with the technical specifications. These findings indicated poor heat treatment quality. - Hardness Testing
Hardness gradient testing was performed on the left and right tooth surfaces of the planetary gear. The results showed that the carburized layer depths on both sides were within the design requirements (2.16 – 2.88 mm). However, the overall hardness profile and the lower surface hardness values were consistent with the metallographic examination results, suggesting that the heat treatment process did not achieve the desired hardness distribution. - Scanning Electron Microscopy (SEM) Analysis
SEM analysis of the spalled surface revealed that the large spalling pits were formed by the propagation of cracks initiated from the surface. The crack origin was located on the tooth surface, and there was no evidence of metallurgical defects in the raw material. The presence of fatigue striations in some areas of the spalled surface indicated that fatigue was a contributing factor to the failure. - Precision Detection
The dimensional accuracy of the planetary gear was measured using a coordinate measuring machine. The results showed that the gear’s machining accuracy in the free state met the drawing requirements. However, the right tooth surface, which was in contact with the sun gear, exhibited relatively severe wear, with a wear depth of approximately 10.6 μm. - Operation and Maintenance Analysis
- Temperature Monitoring: The temperature of the wind turbine during operation was within the normal range, but there was a slight increase in the gearbox oil temperature. This was attributed to the accumulation of debris from the spalling in the oil circuit, which reduced the lubricant volume and led to increased friction and heat generation.
- Oil Pressure Analysis: The oil pressures at the various lubrication points in the gearbox, including those for the main bearing and the planetary gears, were all within the normal operating range, indicating that the lubrication system was functioning properly in terms of pressure.
(3) Failure Cause Determination
Based on the comprehensive analysis of the inspection results, it was concluded that the spalling of the third – stage planetary gear was primarily due to poor heat treatment quality. The non – compliance of the tooth surface hardness, internal oxidation depth, martensite level, and residual austenite level with the design requirements reduced the contact strength of the gear teeth and shortened the gear’s service life. Although the gearbox was designed and manufactured to meet the necessary technical standards, and the operating conditions and maintenance were generally within normal limits, the substandard heat treatment process was the root cause of this particular failure.
6. Prevention and Mitigation Measures
(1) Quality Control in Material Selection and Manufacturing
- Stringent Material Inspection
To ensure the quality of the gear material, comprehensive inspection procedures should be implemented. This includes strict control of the chemical composition, microstructure, and mechanical properties of the raw materials. Incoming materials should be tested using advanced analytical techniques such as spectroscopy and metallography to verify compliance with the specified standards. Any material that fails to meet the requirements should be rejected. - Optimization of Manufacturing Processes
- Forging Optimization: The forging process should be carefully controlled to ensure proper shaping of the gear blank and a uniform grain structure. This can be achieved through the use of advanced forging techniques, such as precision forging and isothermal forging, which can minimize the formation of defects and improve the material’s mechanical properties.
- Machining Precision Improvement: Investment in high – precision machining equipment and the implementation of strict quality control measures during machining are essential. Advanced machining technologies, such as computer – numerical – control (CNC) machining and grinding, can be employed to achieve accurate gear tooth profiles and tight dimensional tolerances. Regular inspection and calibration of machining tools are also necessary to maintain machining accuracy.
- Heat Treatment Process Optimization: The heat treatment process should be optimized to ensure the desired microstructure and mechanical properties. This involves precise control of parameters such as heating rate, quenching temperature, and tempering time. The use of advanced heat treatment furnaces with temperature and atmosphere control capabilities can help achieve more consistent and reliable heat treatment results. Additionally, post – heat treatment inspection and testing, such as hardness testing and metallographic analysis, should be carried out to verify the quality of the heat – treated gears.
(2) Enhanced Monitoring and Maintenance Strategies
- Condition Monitoring Systems
Installing advanced condition monitoring systems on wind turbines can provide real – time data on the gearbox’s operating conditions. These systems can monitor parameters such as vibration, temperature, oil quality, and wear debris in the lubricant. By analyzing this data, potential gear damage can be detected at an early stage, allowing for timely maintenance and repair actions. For example, vibration analysis can identify changes in the gear’s dynamic characteristics, which may indicate the presence of damage such as pitting or misalignment. - Regular Maintenance Schedules
Establishing a comprehensive and regular maintenance schedule is crucial for ensuring the long – term reliability of the gearbox. Maintenance activities should include routine inspections of the gearbox components, replacement of worn or damaged parts, and lubricant analysis and replacement. Lubricant should be sampled and tested regularly to check for contamination, degradation, and proper viscosity. If any abnormalities are detected, the lubricant should be replaced promptly to prevent lubrication – related failures. - Predictive Maintenance
Utilizing predictive maintenance techniques, such as data analytics and machine learning algorithms, can further enhance the effectiveness of maintenance strategies. By analyzing historical and real – time data from the condition monitoring systems, predictive models can be developed to forecast the remaining useful life of the gearbox components and predict potential failures. This allows for proactive maintenance planning, reducing unplanned downtime and optimizing maintenance costs.
(3) Design Improvements
- Gear Design Optimization
The design of the gears can be optimized to improve their load – carrying capacity and resistance to damage. This can involve modifications to the gear tooth profile, such as the use of optimized involute profiles or special tooth geometries that can reduce contact stresses and improve load distribution. Additionally, increasing the gear module or the number of teeth can enhance the gear’s strength and durability. - System – Level Design Considerations
At the system level, considerations can be given to improving the overall reliability and performance of the wind turbine gearbox. This may include the design of more efficient lubrication systems, better sealing to prevent contamination, and the use of advanced materials and coatings for improved corrosion and wear resistance. For example, the use of ceramic coatings on the gear surfaces can reduce friction and wear, while also providing enhanced corrosion protection.
7. Conclusion
Gear damage in wind turbine gearboxes is a complex issue that can have significant implications for the performance and reliability of wind turbines. By understanding the various causes of gear damage, including material factors, manufacturing process defects, operating conditions, and environmental factors, appropriate preventive and mitigation measures can be implemented. Stringent quality control in material selection and manufacturing, enhanced monitoring and maintenance strategies, and design improvements are all essential for reducing the occurrence of gear damage and ensuring the long – term operation of wind turbines. Through continuous research and development, as well as the application of advanced technologies and best practices, the reliability and durability of wind turbine gearboxes can be further enhanced, contributing to the sustainable growth of the wind energy industry.
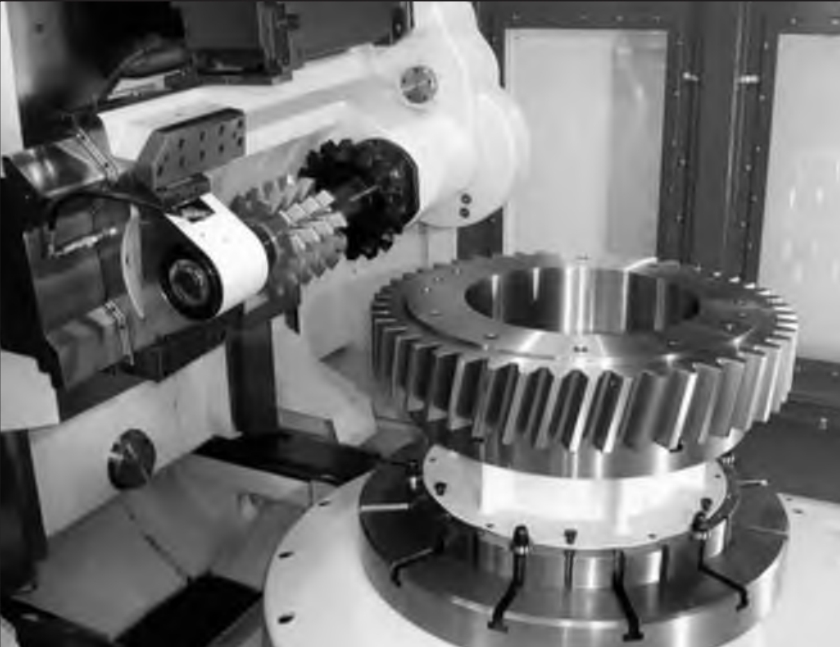