Gear transmission systems are widely used in various fields, but they are prone to faults, especially tooth root cracks. This article focuses on analyzing the vibration response of gear systems with tooth root cracks. It first modifies the potential energy method to calculate the time-varying meshing stiffness more accurately, considering the influence of crack parameters. Then, a 6-degree-of-freedom dynamic model of the gear system is established, taking into account comprehensive meshing errors. The vibration response characteristics of the cracked gear system under stable and variable load conditions are studied, and the sensitivity of the crack gear vibration signal is analyzed using five statistical indicators. The results show that the meshing stiffness decreases with the increase of crack depth and angle, and the crack depth has a greater impact. The periodic impact in the time domain and the sidebands around the meshing frequency and its harmonics in the frequency domain are positively correlated with the crack extension. Under variable load conditions, the vibration signal is similar to the load fluctuation trend, and the low-frequency component is related to the load. The larger the load fluctuation amplitude, the less obvious the fault characteristics. The kurtosis is the most sensitive to the cracked gear vibration signal.
1. Introduction
Gear transmission systems play a crucial role in many industries such as wind power generation and aerospace. However, due to complex working conditions, they are susceptible to faults. Tooth root cracks are a common type of fault, which can lead to gear failure if not detected and repaired in time. Understanding the vibration response of gear systems with tooth root cracks is essential for fault diagnosis and system maintenance.
1.1 Research Significance
The study of the vibration response of gear systems with tooth root cracks is of great significance in the field of mechanical engineering. It helps to improve the reliability and safety of gear transmission systems, reduce maintenance costs, and extend the service life of equipment. By analyzing the vibration characteristics, we can detect and diagnose gear faults in a timely manner, thereby preventing catastrophic failures.
1.2 Research Status at Home and Abroad
Many scholars have conducted extensive research on gear system dynamics and fault diagnosis. In terms of meshing stiffness calculation, methods such as the finite element method, potential energy method, and Ishikawa method have been proposed. The potential energy method is widely used due to its simplicity and efficiency. In the study of the vibration response of cracked gears, various models and analysis methods have been developed. However, most of the previous studies focused on stable working conditions, and the research on the vibration response of gear systems under variable load conditions is relatively insufficient.
2. Time-Varying Meshing Stiffness Calculation Model
The time-varying meshing stiffness is the most important internal excitation in the gear system, and its accurate calculation is crucial for the reliability of dynamic analysis.
2.1 Healthy Gear Meshing Stiffness Calculation Model
2.1.1 Modification of the Potential Energy Method
The traditional potential energy method only considers the deformation energy of the contact between teeth on the base circle. To improve the accuracy of gear modeling, this article modifies the potential energy method by simplifying the part between the root circle and the base circle as a straight line for calculation. The formulas for calculating the bending energy, compression energy, and shear energy are revised accordingly. The specific formulas are as follows:
where is the force acting on the meshing point, which can be decomposed into radial force and tangential force ; and are the base circle radius and root circle radius respectively; is the elastic modulus; is the shear modulus; is the Poisson’s ratio; and are the moments of inertia of the gear section at distances and from the base circle respectively; and are the cross-sectional areas; is the distance from the meshing point to the base circle; is the distance from the meshing point to the tooth centerline; is the height of the section at a distance from the base circle; is the half-tooth angle on the base circle, and is the approximate half-tooth angle on the root circle.
2.1.2 Verification of the Modified Potential Energy Method
The ISO 6336-1-2006 standard provides a method for calculating the meshing stiffness of gears. The maximum single-tooth meshing stiffness calculated by this standard is , and the average meshing stiffness of the teeth is , where is the theoretical single-tooth meshing stiffness, the theoretical correction coefficient , the gear base structure parameter , the basic tooth profile coefficient , is the gear helix angle, and is the gear contact ratio.
To verify the effectiveness of the stiffness calculation method in this article, the potential energy method is denoted as Method A, the method in this article is denoted as Method B, and the results calculated according to the ISO standard are used for comparison. The comparison results of the maximum single-tooth meshing stiffness and the average time-varying meshing stiffness calculated by the two methods and the error with the ISO standard calculation value are shown in the following table:
Method | Maximum Single-Tooth Meshing Stiffness ( N/m) | Relative Error with ISO Standard (%) | Average Time-Varying Meshing Stiffness ( N/m) | Relative Error with ISO Standard (%) |
---|---|---|---|---|
ISO Standard | 1.84 | 0 | 2.89 | 0 |
Method A | 2.34 | 27.17 | 3.73 | 29.07 |
Method B | 1.98 | 7.61 | 3.1 | 7.27 |
It can be seen from the table that Method A ignores the deformation energy between the base circle and the root circle, resulting in a larger calculated stiffness value. The maximum error of the single-tooth meshing stiffness is 27.17%, and the average meshing stiffness error is 29.07%. Method B supplements the calculation of the deformation energy between the root circle and the base circle, and the maximum error of the single-tooth meshing stiffness is 7.61%, and the average meshing stiffness error with the ISO standard is 7.27%. This effectively improves the accuracy of the gear model and verifies the effectiveness of the stiffness calculation and analysis in this article.
2.2 Cracked Gear Meshing Stiffness Calculation Model
Gear tooth roots are prone to cracks due to pulsating cyclic contact stress. In this article, it is assumed that the crack is a through crack, and the crack propagation line is symmetrically distributed with respect to the tooth centerline, and the crack propagation limit line is a straight line.
The geometric model of the tooth root crack is shown in Figure 3. is the initial crack depth that does not reach the tooth centerline, is the crack length that exceeds the tooth centerline as the gear crack propagates, the total crack length , is the maximum depth when the crack propagates to the tooth centerline, and is the crack propagation angle.
Due to the failure of the area enclosed by the crack propagation line, limit line, and tooth profile line, the effective cross-sectional area and moment of inertia at the meshing point decrease. Therefore, according to the different crack propagation depths, the crack calculation model is divided into the following three cases. Models 1 and 2 correspond to the crack propagation depth less than 50% (measured by the percentage of in to measure the degree of tooth root crack propagation), and Models 3 and 4 correspond to the crack propagation depth greater than 50%.
where , .
2.3 Influence Mechanism of Crack Parameters on Time-Varying Meshing Stiffness
To study the influence law of crack parameters on the time-varying meshing stiffness of gears, based on the above cracked gear meshing stiffness calculation model and combined with the gear pair parameters in Table 1, the stiffness under different crack states is calculated and analyzed.
2.3.1 Changing Crack Depth
Set the crack angle to 45 degrees and change the crack propagation depth to 10%, 25%, 50%, and 70%. As shown in Figure 4, when the crack depth is small, the decrease in the time-varying meshing stiffness is relatively small, and the stiffness decrease in the second double-tooth meshing region is more significant than that in the first double-tooth region。
3. Dynamic Model of Gear System with Tooth Root Cracks
3.1 Gear System Dynamic Modeling
Based on the above analytical model of the time-varying meshing stiffness of the gear, considering the comprehensive meshing error factor and taking into account the three degrees of freedom in the transverse, longitudinal, and torsional directions, a 6-degree-of-freedom dynamic model of the gear transmission system is established using the lumped parameter method as shown in Figure 6.
In Figure 6: and are the masses of the driving gear and the driven gear respectively; and are the moments of inertia of the driving gear and the driven gear respectively; , and , are the support stiffnesses of the driving gear and the driven gear in the x and y directions respectively; , and , are the support damping of the driving gear and the driven gear in the x and y directions respectively; is the driving torque; is the load torque; and are the base circle radii; and are the torsional direction line displacements; is the meshing damping; is the time-varying meshing stiffness of the gear.
According to the Lagrange energy method, the dynamic equations of the gear system are derived as follows:
where is the relative displacement of the gear along the meshing line direction, and its expression is:
The time-varying meshing damping of the gear pair can be expressed as:
where is the meshing damping ratio, generally taken as 0.03 – 0.17.
For the convenience of calculation, the simplified comprehensive meshing error formula is:
where is the mean value of the transmission error, is the coefficient of the first harmonic term, is the meshing frequency, and is the initial phase angle of the first harmonic.
The gear parameters used in the dynamic model are shown in the following table:
3.2 Solution of the Dynamic Model of the Gear System with Tooth Root Cracks
Set the torque applied to the driving gear to 100N·m, the load torque on the driven gear to 250N·m, the rotational speed of the driving gear to 1500r/min, the rotational frequency of the small gear , the rotational frequency of the large gear , and the meshing frequency . Assume that there is a crack fault at the tooth root of the driving gear, and the characteristic frequency of the fault is the rotational frequency of the driving gear .
To study the dynamic characteristics of the gear system under crack fault conditions, according to the gear parameters in Tables 1 and 3, the influence of the tooth root crack model on the effective cross-sectional area and moment of inertia is introduced into the expressions of bending stiffness and shear stiffness. Then, through the above modified time-varying meshing stiffness calculation model, the time-varying meshing stiffness under different crack parameters is obtained.
This factor is introduced into the above gear system dynamic model, and the Newmark-β method is used to solve the dynamic equations of the gear system to finally obtain the vibration response of the gear system. The flowchart of the dynamic analysis of the gear system with crack faults is shown in Figure 7.
4. Dynamic Simulation and Vibration Response Analysis
4.1 Vibration Response of Cracked Gear under Stable Working Conditions
4.1.1 Vibration Response of Healthy Gear
When there is no crack, the vibration response of the gear system is shown in Figure 8. It can be seen that the time-domain signal of the gear system in the healthy state is relatively stable, and only the amplitude spectrum centered around the meshing frequency and its harmonics exists in the frequency domain.
4.1.2 Vibration Response of Cracked Gear
To study the influence law of cracks on the dynamic response characteristics of the gear system, set the crack angle to 45° and divide the crack depth into four cases: 0.42mm (10%), 1.05mm (25%), 2.1mm (50%), and 2.94mm (70%). Calculate the vibration responses of the gear system under different crack parameters. Figures 9 and 10 show the time-domain vibration displacement and frequency-domain response diagrams of the gear system in the y direction under different crack parameters.
When a crack occurs at the tooth root, a periodic impact will be generated in the vibration signal in the time domain, and the period is the time required for the faulty gear to rotate one week. Observing Figure 9, it can be seen that as the crack depth increases, the periodic impact becomes larger and larger. When the crack propagation does not exceed the tooth centerline (crack propagation depth less than 50%), the impact phenomenon caused by the crack is not obvious; when the crack propagation exceeds the tooth centerline (crack propagation depth greater than 50%), the impact phenomenon of the signal caused by the crack is very obvious, and as the crack continues to expand, the impact amplitude increases sharply.
In the frequency domain, by comparing the vibration signals in the healthy state and under different degrees of cracks, it is found that when a crack occurs, corresponding sideband components appear near the meshing harmonics. Observing Figure 10, it can be seen that when the crack propagation degree is small (crack propagation depth less than 50%), small 杂频 appear between and , and between and , and the sidebands are not obvious; when the crack propagation degree is large (crack propagation depth greater than 50%), very obvious sidebands with an interval of the fault frequency 25Hz appear near the 3rd, 4th, and 5th harmonics of the meshing frequency, and as the crack depth increases, the amplitude of the sidebands increases significantly.
4.2 Vibration Response of Cracked Gear under Variable Load Conditions
Since the working conditions of the gear transmission system are complex, load torque mutations or fluctuations often occur, which often lead to non-stationary characteristics of the vibration signal and have a certain impact on the fault diagnosis of the gear system. Therefore, based on the above analysis of the vibration response of the gear crack under stable working conditions, this section considers load fluctuations. Assume that the load excitation changes according to the cosine law. Taking a crack with a crack angle of 45° and a crack depth of 50% as an example, the vibration response characteristics of the cracked gear under load fluctuation conditions are studied.
4.2.1 Vibration Response of Healthy Gear under Load Fluctuation
Figure 11 shows the vibration response of the healthy gear system under the load torque . It can be seen from the figure that the vibration signal of the gear system has a similar fluctuation trend to the load excitation, and there is an impact at the low frequency, and the frequency is consistent with the load fluctuation frequency. There are no sidebands near the meshing frequency and its harmonics. Compared with the vibration response of the healthy gear system under stable working conditions in Figure 8, it can be known that the impact at the low frequency is caused by the load fluctuation.
4.2.2 Vibration Response of Cracked Gear under Load Fluctuation
Set the load torque to and perform dynamic simulation. Figure 12 shows the vibration response of the gear system under this load. Observing the time-domain diagram, it can be seen that the signal modulation phenomenon is obvious, and the impact of the crack fault on the signal is relatively obvious. Observing the frequency-domain diagram, it can be seen that since the load torque fluctuation frequency is 10Hz and the crack fault frequency is 25Hz, sidebands with intervals of 10Hz and 25Hz appear around the 3rd, 4th, and 5th harmonics of the meshing frequency.
Increase the fluctuation amplitude of the load torque and set the load torque to . Perform dynamic simulation. Figure 13 shows the vibration response of the gear system under this load. Observing the time-domain diagram, it can be seen that the amplitude of the vibration signal of the gear system increases, and some impact phenomena caused by the crack fault are weakened. Observing the frequency-domain diagram, it can be seen that the impact amplitude caused by the load at the low frequency increases significantly; the amplitude of the sidebands with the load frequency interval near the meshing harmonics increases, and the amplitude of the fault sidebands decreases.
Continue to increase the fluctuation amplitude of the load torque and set the load torque to . Perform dynamic simulation. Figure 14 shows the vibration response of the gear system under this load. Observing the time-domain diagram, it can be seen that the amplitude of the vibration signal of the gear system continues to increase, and some impacts caused by the crack fault in the time domain are “submerged”. Observing the frequency-domain diagram, it can be seen that the impact amplitude caused by the load fluctuation at the low frequency continues to increase; the amplitude of the sidebands with the load frequency interval around the meshing frequency continues to increase, and the amplitude of the fault sidebands continues to decrease, and the fault characteristics become less and less obvious.
4.3 Fault Indicator Analysis
To measure the influence of different crack degrees on the fault characteristics, five statistical indicators based on the time-domain vibration signal are used: root mean square, kurtosis, shape factor, impulse factor, and crest factor to evaluate the vibration level of the gear system. Since the magnitudes of each indicator are different, the original indicators are converted into relative increments, and the formula is as follows:
where represents the relative increment of the vibration displacement statistical indicator of the -th crack parameter after conversion; represents the vibration displacement statistical indicator of the -th crack parameter; represents the vibration displacement statistical indicator of the healthy gear.
Figure 15 shows the relative increments of each indicator under the tooth root crack state after conversion. It can be seen from the figure that as the crack degree deepens, all five statistical indicators show a gradually increasing trend, but the increasing speed is different. When the crack depth is small, the trend of each indicator is relatively stable, indicating that it is not very sensitive to small early cracks; when the crack depth exceeds 50%, the kurtosis, crest factor, and impulse factor show an obvious growth trend, which is caused by the intensified deformation when the crack propagates beyond the tooth centerline, and among them, the kurtosis index increases the most obviously. When the crack angle is small, the change of each indicator is weak. When the crack angle is greater than 45 degrees, the kurtosis and impulse factor increase significantly, and the kurtosis increases the fastest. In summary, the kurtosis is the most sensitive to the crack propagation.
5. Conclusions
In this article, the potential energy method is appropriately modified and verified using the ISO 6336-1-2006 standard. A full-depth tooth root crack model is established to analyze the influence mechanism of crack parameters on the gear meshing stiffness. Based on this stiffness analytical model, a dynamic model of the gear system with tooth root cracks is established to analyze the vibration response characteristics of the cracked gear under stable and variable load conditions. At the same time, different signal indicators are used to analyze the sensitivity of the tooth root crack.
- As the crack depth and angle increase, the meshing stiffness decreases, and the crack depth has a greater impact.
- As the crack propagates, the periodic impact phenomenon in the vibration signal in the time domain intensifies, and the amplitude of the sidebands generated around the 3rd, 4th, and 5th harmonics of the meshing frequency in the frequency domain increases significantly; under variable load conditions, the waveform of the vibration signal is similar to the load fluctuation trend, and the impact at the low frequency is related to the load. The larger the load fluctuation amplitude, the larger the impact at the low frequency, the less obvious the impact caused by the crack, and the sidebands at the meshing frequency and its harmonics gradually decrease, and the fault characteristics become less and less obvious.
- As the crack propagates, the relative increments of the kurtosis and impulse factor of the gear vibration displacement signal both increase significantly, but the kurtosis index is the most sensitive to the vibration signal of the cracked gear.
Future research can focus on further improving the accuracy of the crack model and considering more complex working conditions to provide more accurate theoretical support for the fault diagnosis and maintenance of gear systems.
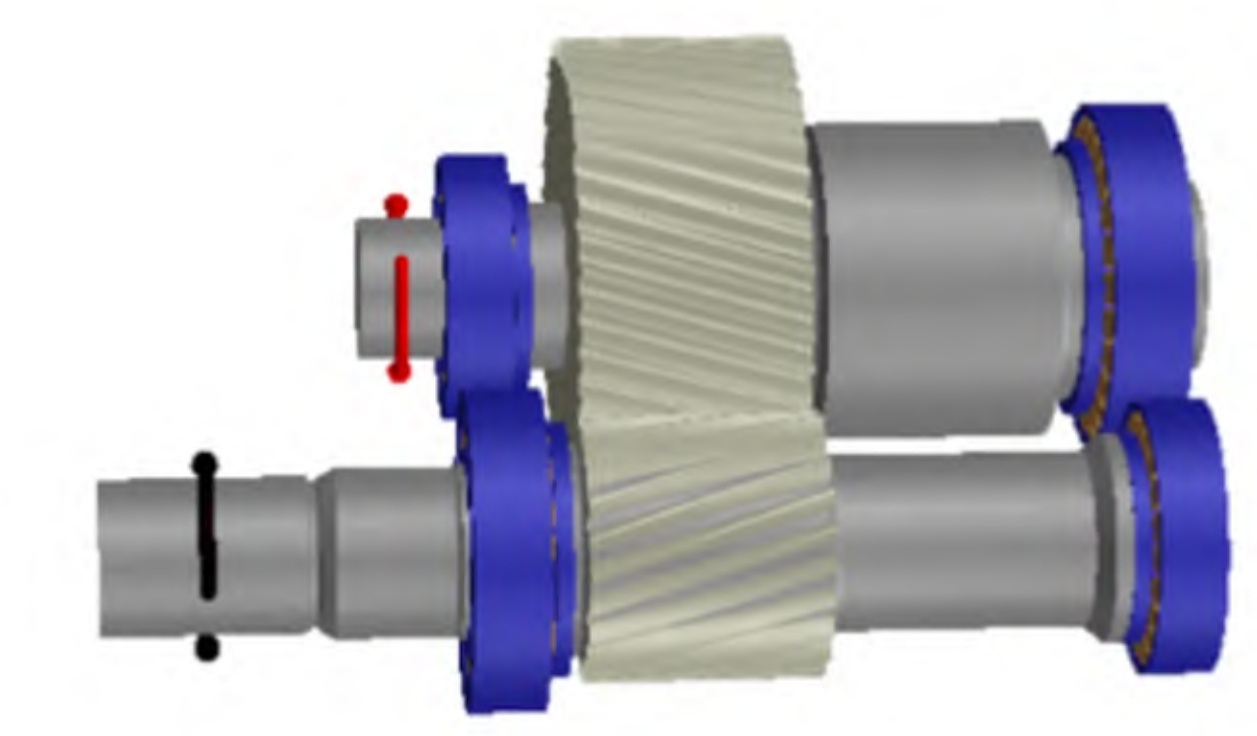