Gear shafts are important parts that support rotating parts and rotate with them to transmit motion, torque, or bending moments. They are required to have strong load-bearing capacity High transmission efficiency, stable transmission, and long service life are the characteristics of the gear shaft. Failure of the gear shaft can lead to reduced system transmission accuracy, decreased transmission efficiency, increased noise and vibration, and further spread of faults, which can affect the operation of other key components and lead to equipment downtime and the entire system being paralyzed. Analyzing the problem of gear shaft failure, identifying the cause of failure, and proposing preventive measures can prevent the recurrence of similar failures and is of great significance for the safe operation of equipment. The problem of gear shaft failure has been studied and reported extensively, mainly focusing on cracking or fracture failures caused by improper heat treatment processes, processing defects, and foreign object sticking. These studies have laid a good foundation for improving the quality of gear shafts and handling failures. However, there are few reports on the hydrogen embrittlement failure of gear shafts. A gear shaft made of 1CrNiMo7-6 steel underwent carburizing + quenching + tempering heat treatment and was placed for 5 days before axial cracking occurred. The gear shaft processing process was: normalizing → tempering → turning → carburizing → quenching → low temperature tempering. In order to clarify the nature and cause of the failure of the gear shaft, the macro and microscopic morphology observation and energy spectrum composition analysis were conducted on the fracture surface of the gear shaft, and the microstructure of the material was examined. The hardness and hydrogen content of the material were also tested. On the basis of clarifying the failure mechanism of the gear shaft, corresponding preventive measures were proposed.
Test materials
The macro appearance of the gear shaft fracture was analyzed using a scanning electron microscope, and the microstructure of the gear shaft fracture was analyzed using a field emission scanning electron microscope (FE-SEM) model NOVA NANOSEM 450. The micro-area composition analysis of the gear shaft fracture was performed using an energy spectrometer model OXFORDX-MAX attached to the scanning electron microscope. A cross-sectional sample was cut from the vicinity of the fracture on the gear shaft tooth position, and after grinding and polishing, the surface layer was tested for Vickers hardness using a microscope model Q10A+ with a load weight of 500g. A cross-sectional sample was cut from the vicinity of the fracture on the gear shaft tooth position, and after grinding, polishing, and etching, the microstructure of the surface layer and matrix was observed under an optical microscope model OLYMPUS GX51. Cylindrical samples measuring ϕ5mm×5mm were cut from the near-surface and core of the gear shaft, and hydrogen content was tested using an oxygen nitrogen hydrogen analyzer model ONH836.
Experimental process
The fracture surface of the gear shaft shows cracks originating from the interior of the shaft, with the source region near the bottom of the tooth, approximately 4.5 mm from the surface. The source region has a long strip-shaped defect distributed along the axial direction, with a length of approximately 2.6 mm and a width of approximately 0.28 mm. The micro-morphology of the fracture surface of the gear shaft shows that the high-magnification morphology of the long strip-shaped defect in the source region of the fracture surface is granular, and the fracture surface near the defect and in the early stage of crack propagation exhibits brittle fracture characteristics, i.e., mixed characteristics of crystal + cleavage. Local tearing edges (chicken claw marks) can be seen on the crystal plane. The fracture surface formed in the later stage of crack propagation (far from the defect) mainly exhibits ductile dimple characteristics. The fracture surface of the gear shaft matrix region opened artificially mainly exhibits ductile dimple characteristics.


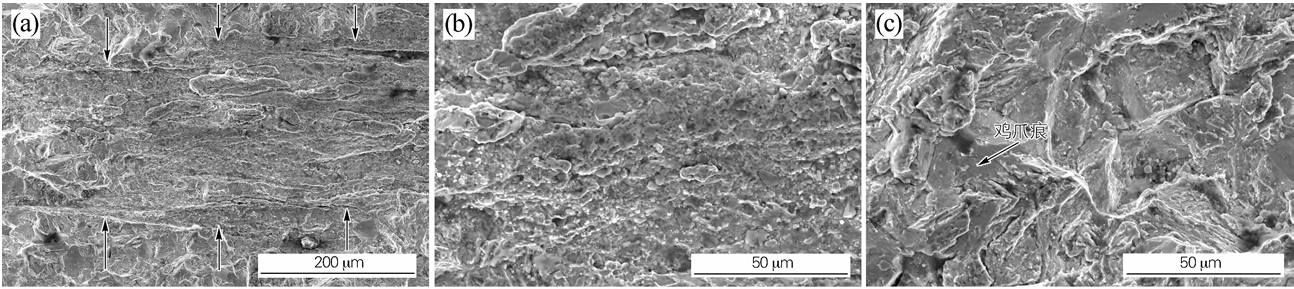
Microstructure inspection
The microstructure of the surface and matrix near the fracture of the tooth position shows that there is no abnormality in the microstructure of the gear shaft matrix and the carburized and hardened layer The body is tempered martensite structure, and no net carbide is found in the carburized and hardened layer.

Gear shaft analysis
The macro and micro morphology observation of the fracture shows that the crack of the gear shaft originated from the internal long strip-shaped defect, and mainly appeared along the fracture source region and the early stage of expansion Crystal + cleavage mixed characteristics. The occurrence of brittle cracking along the crystal of steel parts is usually related to three factors: the high brittleness of the material itself, hydrogen-induced brittle cracking, and stress corrosion cracking. The fracture of the gear shaft substrate is mainly characterized by a tough pit, indicating that the material itself does not exhibit significant brittleness, and the substrate structure near the fracture is not abnormal, thus excluding the possibility of brittle cracking due to the brittleness of the material itself. In addition, the gear shaft cracks from the inside, and there is no obvious corrosion product or corrosive element near the fracture source area and in the early stage of expansion, thus excluding the possibility of stress corrosion cracking. After heat treatment, the gear shaft cracks after a period of time, which is delayed in time. The fracture source area near the gear shaft and in the early stage of expansion mainly exhibit mixed characteristics of crystal + cleavage, with local chicken claw marks visible on crystal faces (a typical characteristic of hydrogen-induced brittle cracking). Based on the above results, it can be determined that the cracking nature of the gear shaft is hydrogen-induced delayed brittle cracking.
The gear shaft undergoes hydrogen embrittlement cracking under the residual stress during the static process. Research shows that after the part is carburized and quenched, the residual stress in the hardened layer is usually compressive stress, and there is a transition zone between the hardened layer and the matrix. The residual stress in the transition zone gradually changes from compressive stress to tensile stress. The crack originates from the inside of the gear shaft, and the crack source region is located near the transition zone of the matrix, where the residual tensile stress is present. There are large-scale long strip alumina inclusions in the source region of the gear shaft. Under the residual tensile stress, the matrix and alumina inclusions separate along the interface to form pores, and the stress concentration on the edge of the pores causes hydrogen atoms in the material to migrate and accumulate around the pores. Although the average hydrogen concentration of the gear shaft matrix is low, the hydrogen concentration around the alumina inclusions increases significantly, leading to hydrogen embrittlement cracking under the residual tensile stress. Figure 7 shows the process of hydrogen atom aggregation near the alumina inclusions and hydrogen-induced crack initiation.
Preventive measures for gear shaft
According to the influencing factors of hydrogen embrittlement failure of steel parts, preventive measures are usually considered from the following three aspects: 1. Reducing the hydrogen content in the material; 2. Adjusting The heat treatment process should be adjusted to reduce the strength of the material; ③ The level of tensile stress should be appropriately reduced. The hydrogen content of the gear shaft matrix is low, and the hardness of the gear shaft matrix meets the technical requirements, so preventive measures can be considered from the perspective of reducing the level of tensile stress. The large-scale strip-like alumina inclusions in the gear shaft cause large stress concentrations, which is the main reason for hydrogen embrittlement cracking. Therefore, the material quality of the gear shaft should be strictly controlled. In addition, the detection of large-scale non-metallic inclusions in the gear shaft should be strengthened. Since the large-scale alumina inclusions in the crack source region are accidental foreign inclusions, rather than endogenous inclusions that are abundant and relatively evenly distributed in the material, accidental foreign inclusions are difficult to detect through conventional metallographic examination. Ultrasonic, eddy current and other nondestructive testing methods can be used for detection.
Conclusion and suggestions for gear shaft
1) The cracking nature of the gear shaft is hydrogen-induced delayed brittle cracking.
2) The large-scale strip-shaped alumina inclusions in the internal matrix of the gear shaft, which lead to large stress concentrations, are the main cause of hydrogen embrittlement cracking.
3) The material of the gear shaft should be strictly controlled. In addition, nondestructive testing methods such as ultrasonic and eddy current can be used to detect large-scale non-metallic inclusions inside the gear shaft It is necessary to conduct inspections to prevent similar failures from occurring.